After-Action Report: Airventure 2025
Hey ya’ll. Its actually the week after Oshkosh AirVenture 2025 and we are all back in the office and shop. Wow, what an Oshkosh! We had a super busy and productive week at the show. Getting there was a challenge, as was getting home. There’s lots to cover, so here goes:
This year, we chose to fly the P-36 in to the show, as the trailer was going to be hauling the P-40 fuselage display frame. The weather was actually cooperating and we started out with haste the morning of Saturday the 19th; the truck hauling the trailer, and the P-36 hauling me. This was all after everyone put in a very late Friday night to finish the P-40 frame and load up the trailer, which is typical for us trying to get everything right and make it to the show on time.
The P-36 was chugging right along and flew great, but I couldn’t say the same for my Dynon/iPad GPS combo. I was struggling with dim screens, dying batteries, loss of connection, and general nonsense almost the entire trip to Oshkosh. Somewhere south of Williamsport, I ran into some very low ceilings and poor visibility conditions. I had to deviate and found the Susquehanna River and an airport runway staring right at me. Just in time! The older fella who ran the FBO knew immediately that this was a P-36 and a Pearl Harbor paint scheme. How? Well, he’s an aviation artist and even had a mural in the pilot’s lounge of Rasmussens’ Pearl Harbor P-36 in a dogfight. What a coincidence - we made his day!
The sky broke and the sun popped out, revealing clearing skies to the West. I was off again before rain stopped me around dinner time over Akron, OH. I picked Wadsworth Airport and set down. My family was driving right along I-76 in the truck and met me a few hours later for a large hotel room. Last room in town - not cheap! But it was awesome to see my family right then. The next day, I was stuck with low ceilings with sucker holes every once in a while, so I stayed put and waited it out. A kind man at Wadsworth asked if I wanted a hangar for the day and night - yes! I was treated to his collection of vintage aircraft projects. He couldn’t have been nicer and I was welcomed to stay the next night at the FBO which I did. I’m happy to say I made many new friends among the CFIs there.
Then I was off again the next morning and winging my way to Oshkosh via the Navy Pier corridor. What a sight! I did the Fisk arrival which was way out of the way. Hardly anyone in sight along the entire route until over Fisk. I landed right before the Monday airshow shut down the airspace - whew! I taxied behind the Follow Me golf cart and they drove me all over the place - finally stopping and asking me where I wanted to go. To my booth by Vans Aircraft! Then taxied back over to the Homebuilts exhibit area as a crowd was gathering to see the P-36 and hear the lovely sound of the Verner radial engine. It was a grand entrance to the show! Then, Bam! The show was on! It started in a frenzy and didn’t let up all week until the last day on Sunday 27th. We had so many excited fans of the project. We had lots of interest, many people signing up for our Beta Builders program, and some even putting money down. Just what we had hoped for!
Our booth had our trailer with an awning, acting as shelter for our desk and table. We had the P-36 out in the corner of the booth space. It was easily seen from a distance being on a corner booth this year instead of burried half way down the aisle. The corner space cost us more money, but it was worth it I believe. This year we also had our P-40 fuselage on a display stand. It didn’t have the skin on it - so you can see the structure and bones of the bird. We added a profile view of the cowling with section slices on one side to show the contours of the machine. This must have struck a nerve as everyone was praising our decision to display it this way. You could see the lines of the machine were very accurate and gave a good sense of size and volume, but you can also see the primary structure inside, which showed off how we can make other WW2 fighter models with this same frame.
We had Vans Aircraft, Sonex, Panther, Stewart 51, Bede and many other companies engineers and sales folks stop by the booth and check out the planes. We showed them everything and let them sit in the P-36. Fun stuff! I finally met Randy Shlitter of Rans Aircraft and had a great time talking aircraft design. Awesome guy! Of course, we also had old friends and customers stop by regularly and we had a wonderful time with them. Excitement was the rule of the day, every day! I want to thank all of you who stopped by our booth; it was a pleasure for us to meet each and every one of you. You are why we are doing this!
I have to say it wasn’t all fun and games. Its a lot of hard work to get there on time, stand in the sun all day and answer a billion questions, then go to dinner and crash; just to do it all again the next day. My crew was tireless and pushed on throughout the week, and I have to give big props to the team as well.
We met the sponsors of our B-17 bomber project for a very nice dinner at our rental house. We spent a wonderful time together reviewing design documents and many family treasures involving the B-17 and their legacy. We are humbled to be a part of this endeavor and hope to bring you along on our journey.
I found out later in the week from a fellow Connecticut EAA member who stopped by that there was going to be a memorial service for Joe Gauthier. Joe was our CT resident DAR: the first DAR in the country! He was one among many distinguished EAAers who passed recently. I had to go to that on Sunday and it was a very appropriate service. Kudos to EAA and Jack Pelton for what he said and how it was arranged. A fantastic missing man tribute, made up of aircraft attending the airshow, topped it off. Sunday was brutally hot and humid, especially compared to the relatively mild rest of the week. I think I got over-heated and had to sit in front of our fan for a long time after getting back from the service.
Then, just as suddenly as it began, it was over. I had to run over to the iFly booth and talk to them about a new GPS system. We had talked earlier in the week, and they said to visit as they were closing for a special opportunity - to purchase their floor model before its full release to the public. We spent hours tearing down the exhibit and packing the trailer up with the P-40 fuselage and our booth supplies. We pushed the P-36 to the grass, then I fired up and joined the conga line to get out after the airshow was over. I departed around 6pm in very hot air and managed to make it down to Chicago and enjoyed a beautiful view of the Navy Pier at sunset. With a wild orange sky and the lights of the city coming on, it was amazing! I landed in Porter County airport after dark. I was grateful to have an air conditioned vestibule to hang in and for my family to rescue me later in the night. Breakfast was at a local restaurant - I was recommended a place called ‘Viking Chili Bowl’. With a name like that, we had to try it!
We had hoped to visit the Champaign Lady, but during breakfast we discovered the museum was, unfortunately, closed on Mondays. Afterward, my family dropped me off and headed for home. I flew to Dayton area to visit a good friend, and Verner customer, Rick Shultz and his Grand Champion 2024 Hatz Classic. All was going quite well.
That is, until 19 miles from Andy Barnhart Memorial Airport, my engine power dropped significantly and started making a terrible racket. I used the Nearest Airport mode on my brand new iFly GPS X7 tablet (while everyone who ordered one had to wait another 3 weeks, I was the first customer to get one right there at the show!) 3.6 miles to Hartzell Airport in Piqua, OH. I made it 3.6 miles to Hartzell Airport in Piqua, OH on partial power. Rick’s good friend and A&P Mike Chappe met me there and we diagnosed an issue with the cylinder. We found a broken rocker arm hold down stud. It had just snapped at the base. We could get the old base out of the head and all the parts were sitting in the valve cover. The valve was not stuck, so we don’t know why this happened. This is the first time this has happened for a Verner engine; lucky me!
Well, I spent the whole week after Oshkosh near New Carlisle, OH with friends and had a great time, enjoying good food and good conversations. I did manage to visit the Champaign Lady after all! Once I fixed up the engine with a borrowed part from another customer, I flew back home on Sunday, August 3rd, with the brand new iFly GPS X7 working perfectly the entire time.
Meanwhile, the family had pushed through and arrived home at 3 AM on Tuesday, the 29th. Troopers! I met and made new friends all along this journey, and I am so thankful for how it all happened. It was a true adventure!
We are all back home again and getting back into the swing of it. Work is never over, so if you haven’t heard from us - please send us an email, call, or text. We are back on the bomber tail parts and finishing up the Beta tail kit planning. Expect more updates shortly.
Sam
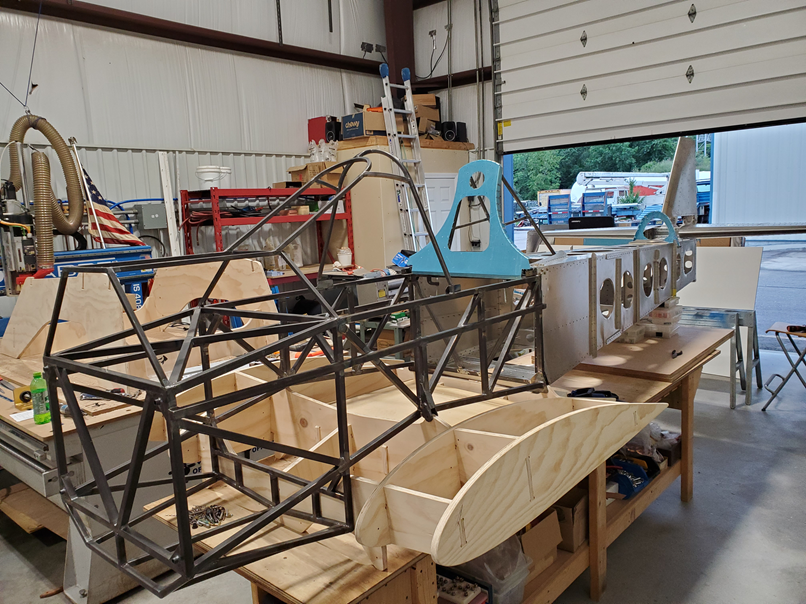


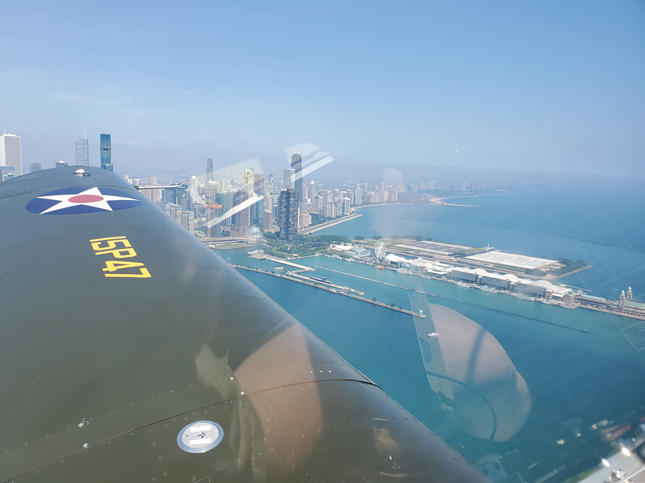
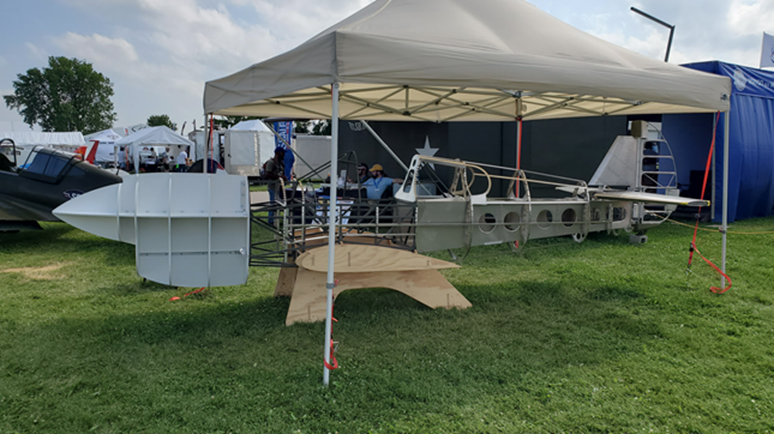

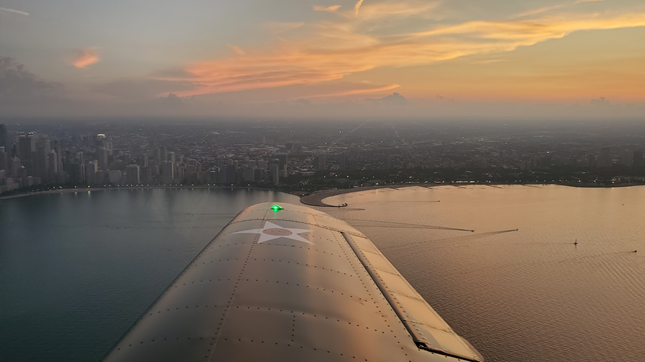
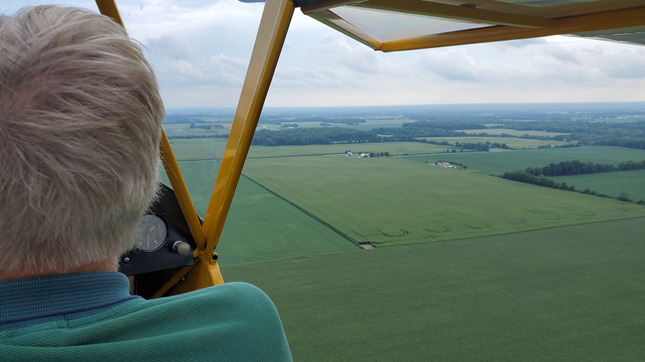
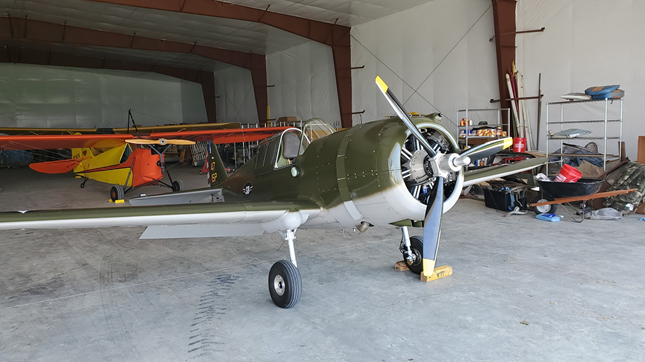
