CNC ROUTER BUILD
The Need for CNC
The original project scope did not account for having an in-house CNC machine. The plan was to outsource material cutting, but that turned out to be a lesson in frustration.
Developing this aircraft using parts from local vendors used to dealing with large serial production contracts was going to be impossible when the design wasn't even complete . This project is "build it as you draw it" and there's no use in waiting for the entire thing to be detailed down to the last rivet before cutting the first blank, there was no way to wait until we had thousands of parts to cut before finding a vendor to cut it all at once. This meant we had to go around the problem, and the solution that makes a lot of sense these days is to go and get a CNC of your own.
So with some research it was decided that the best method was to just go and develop an in-house machine based on some commonly available designs and kits. We already had a 3D printer, and the underlying technology is largely the same, so we thought it wouldn't be terribly difficult to learn.
Well all said and done it all is pretty easy to grasp and understand the result. But there are so many details of design and construction that are not covered in a single source. Lot's of gotchas that are left out of tutorials because the authors took them for granted. Lots of contradictory information. It's a lot like building an airplane.
The Build
The build took about two and a half months of effort before beginning the Hellcat proper; all-told it has easily shown that to be well invested time.
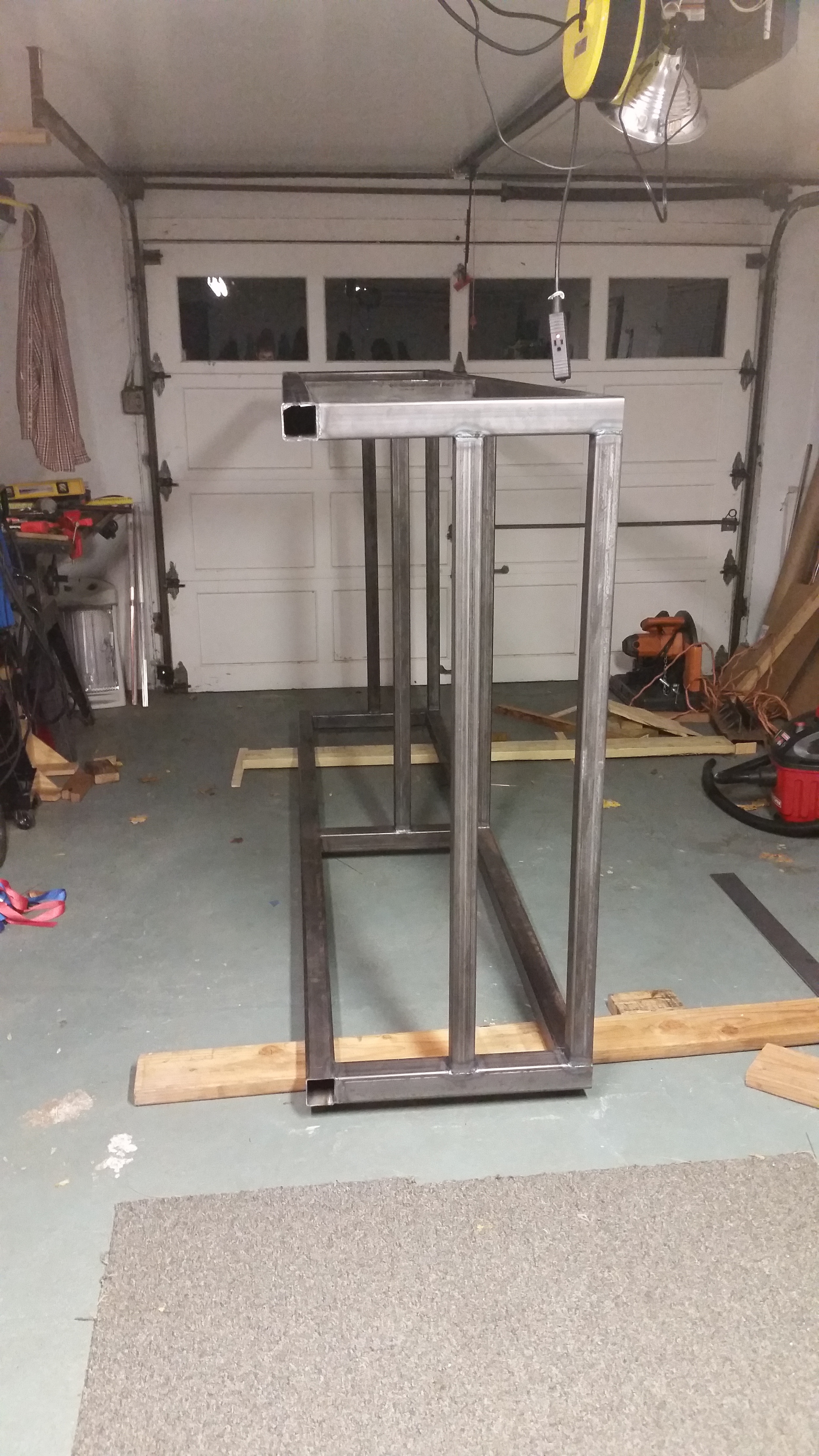
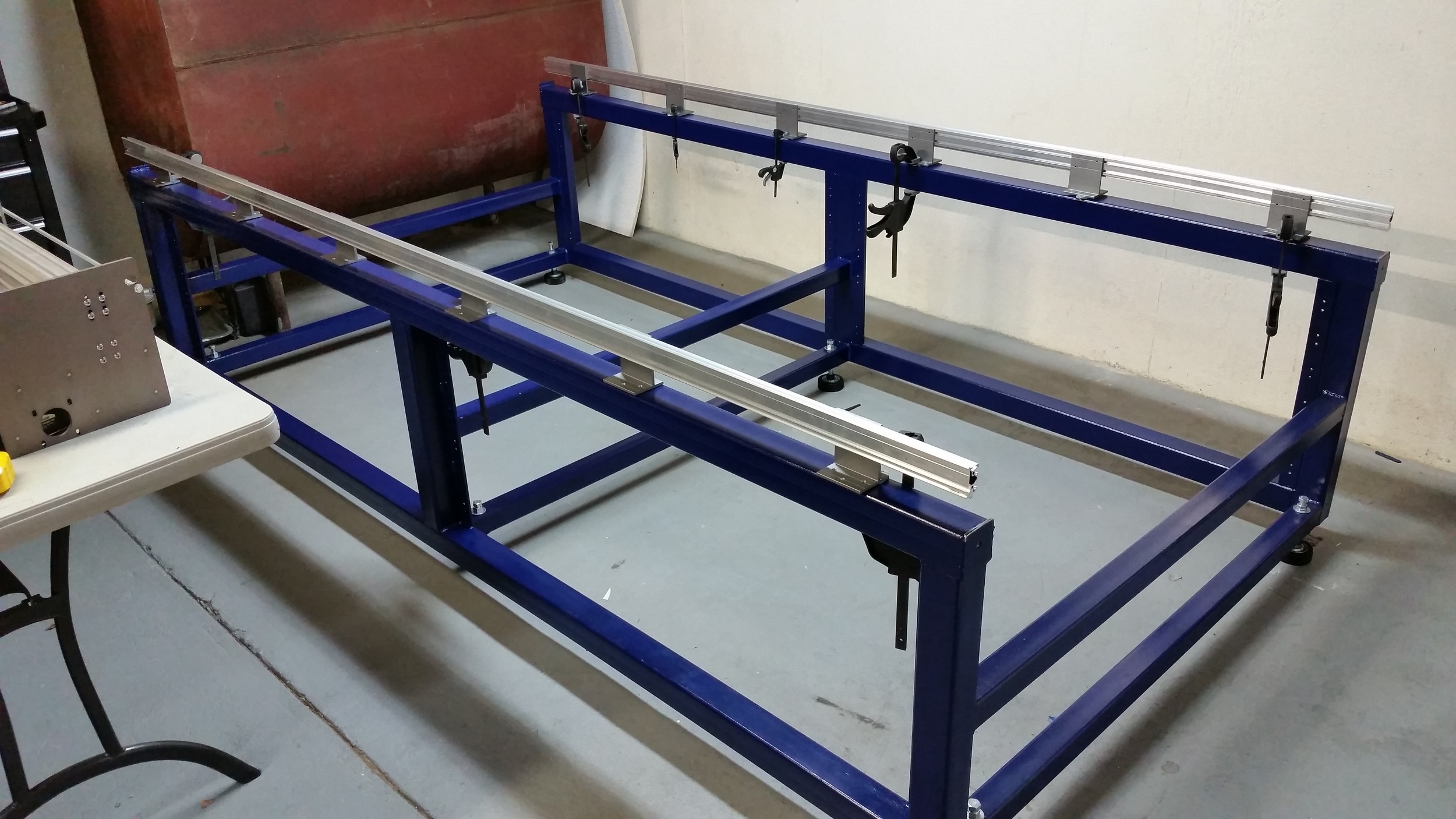
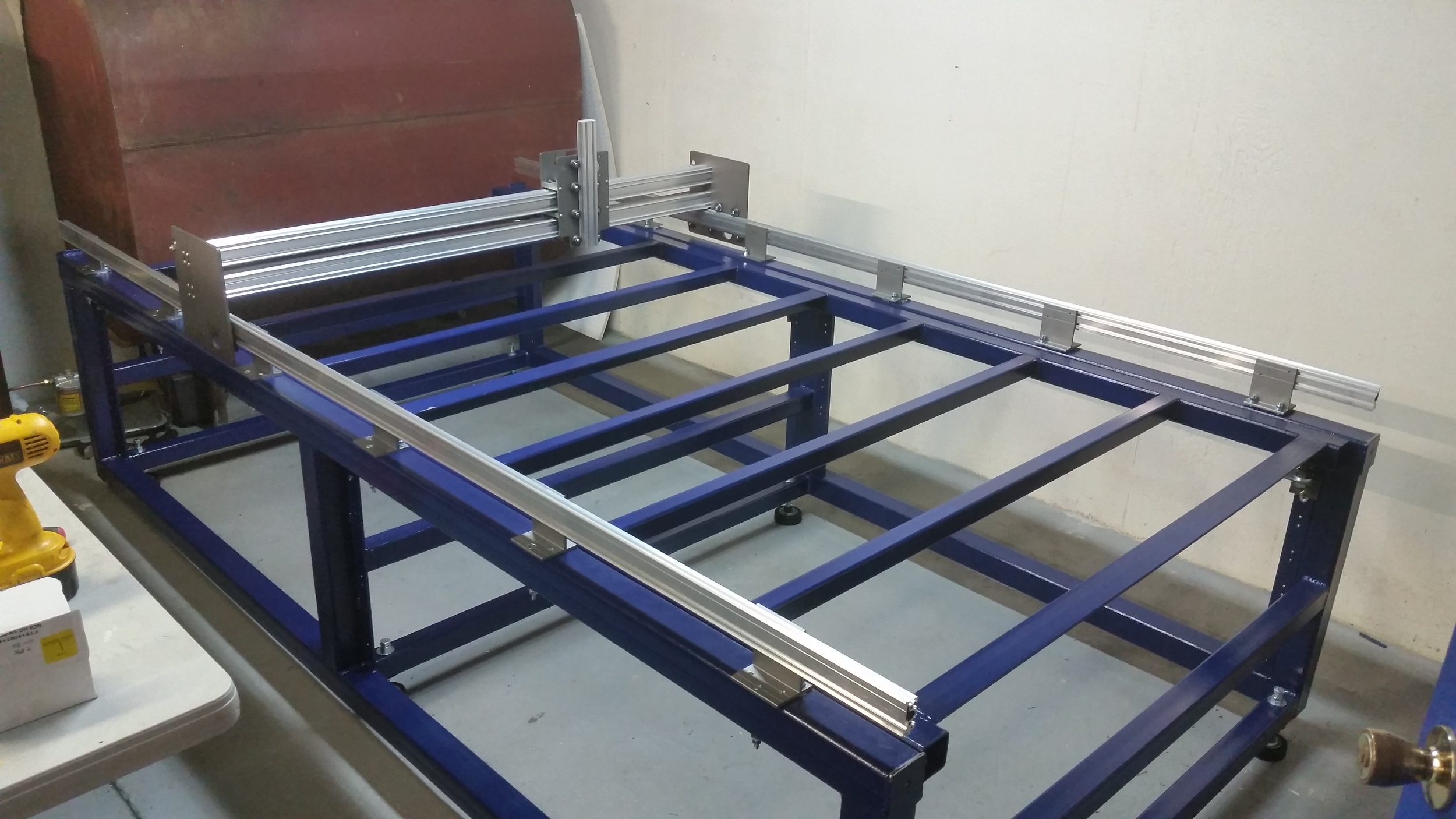
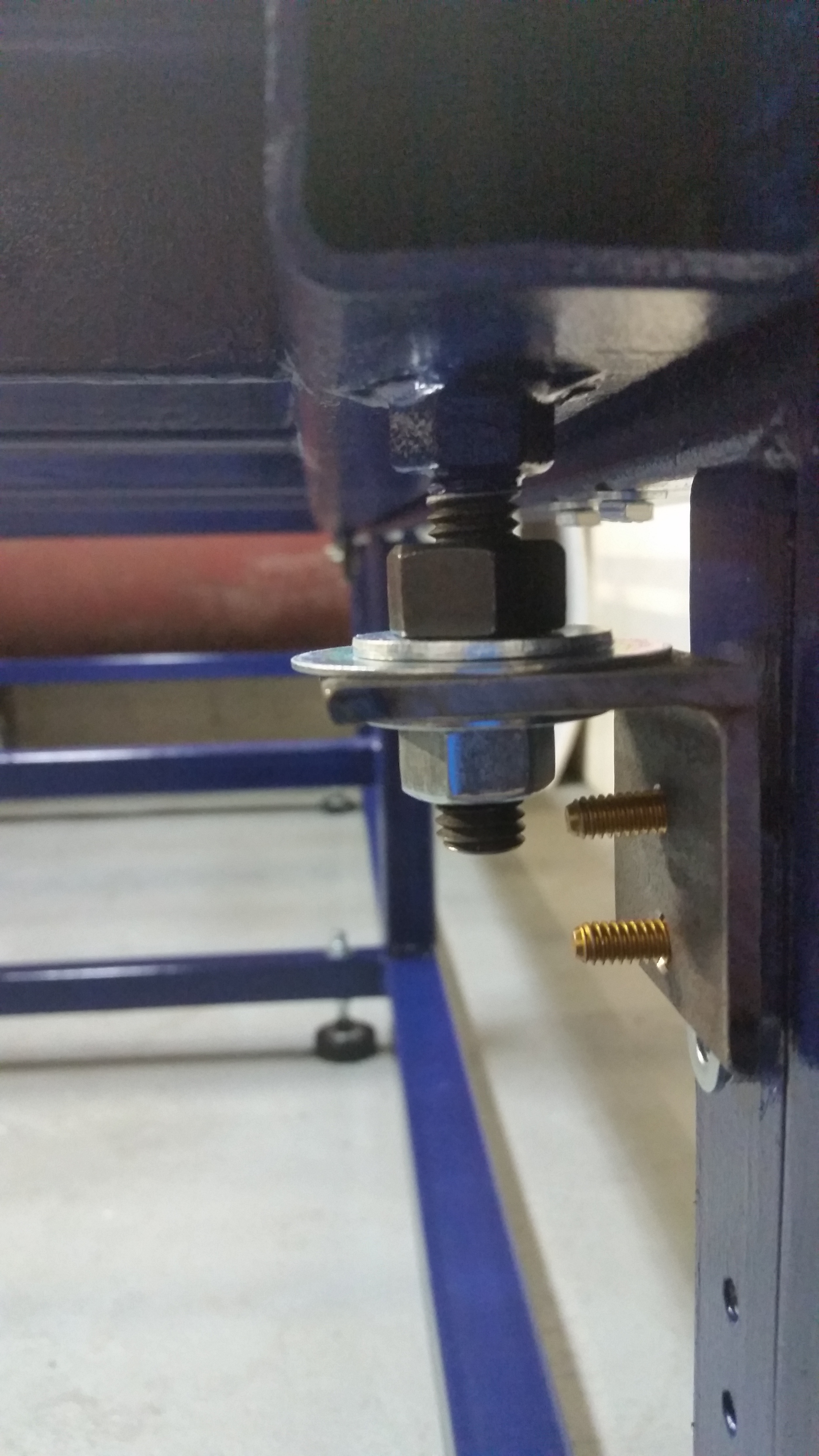
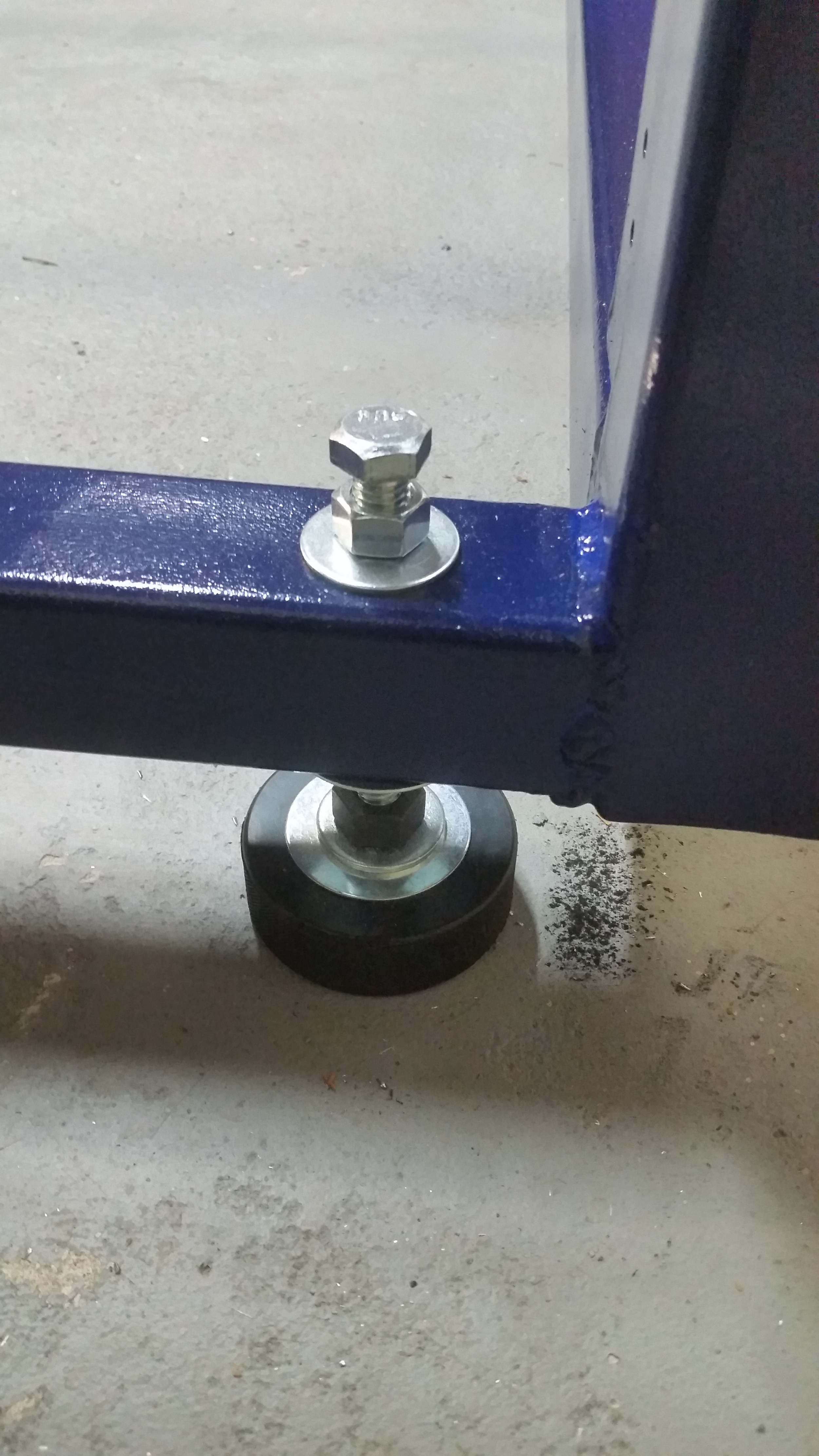
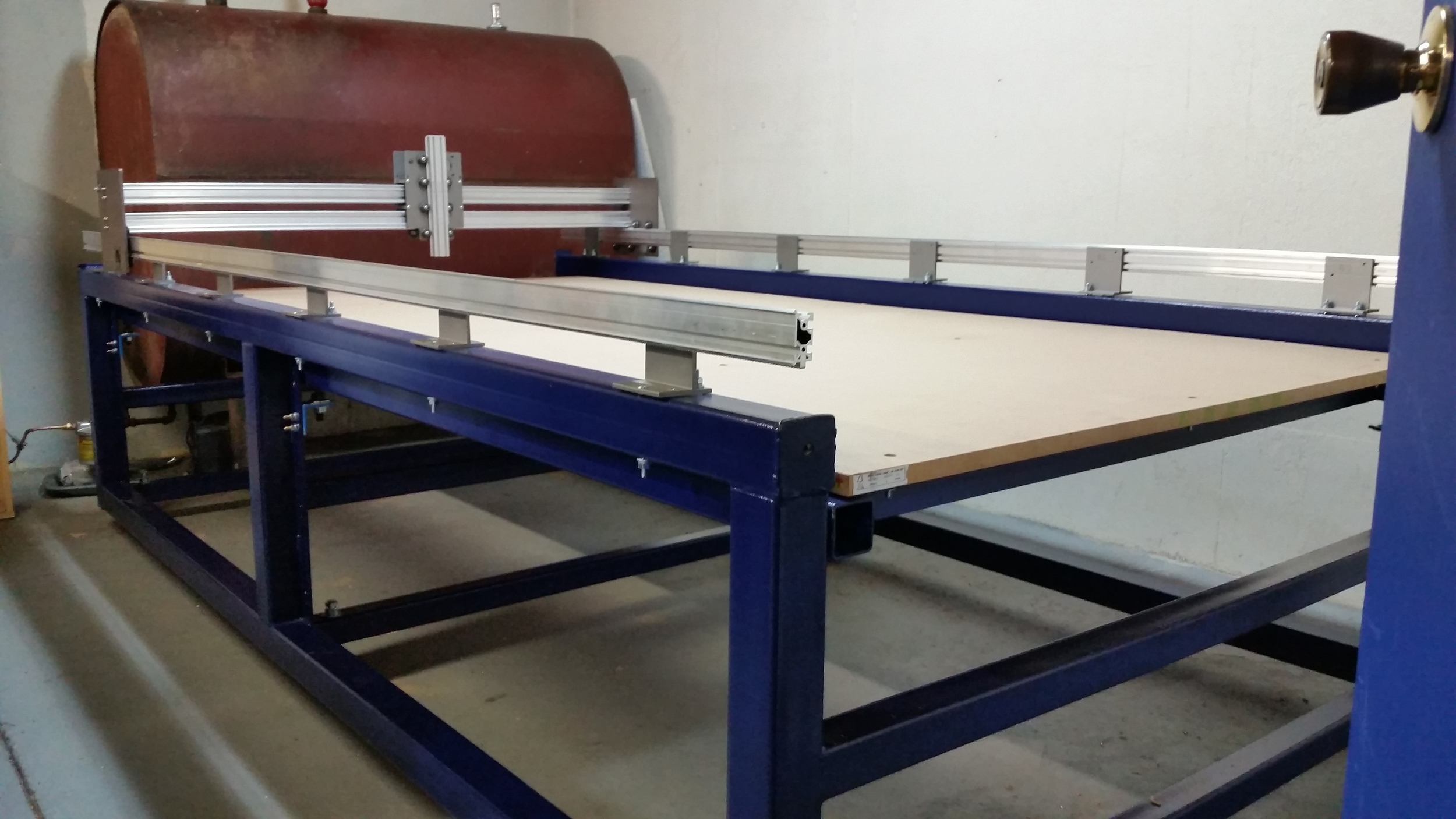
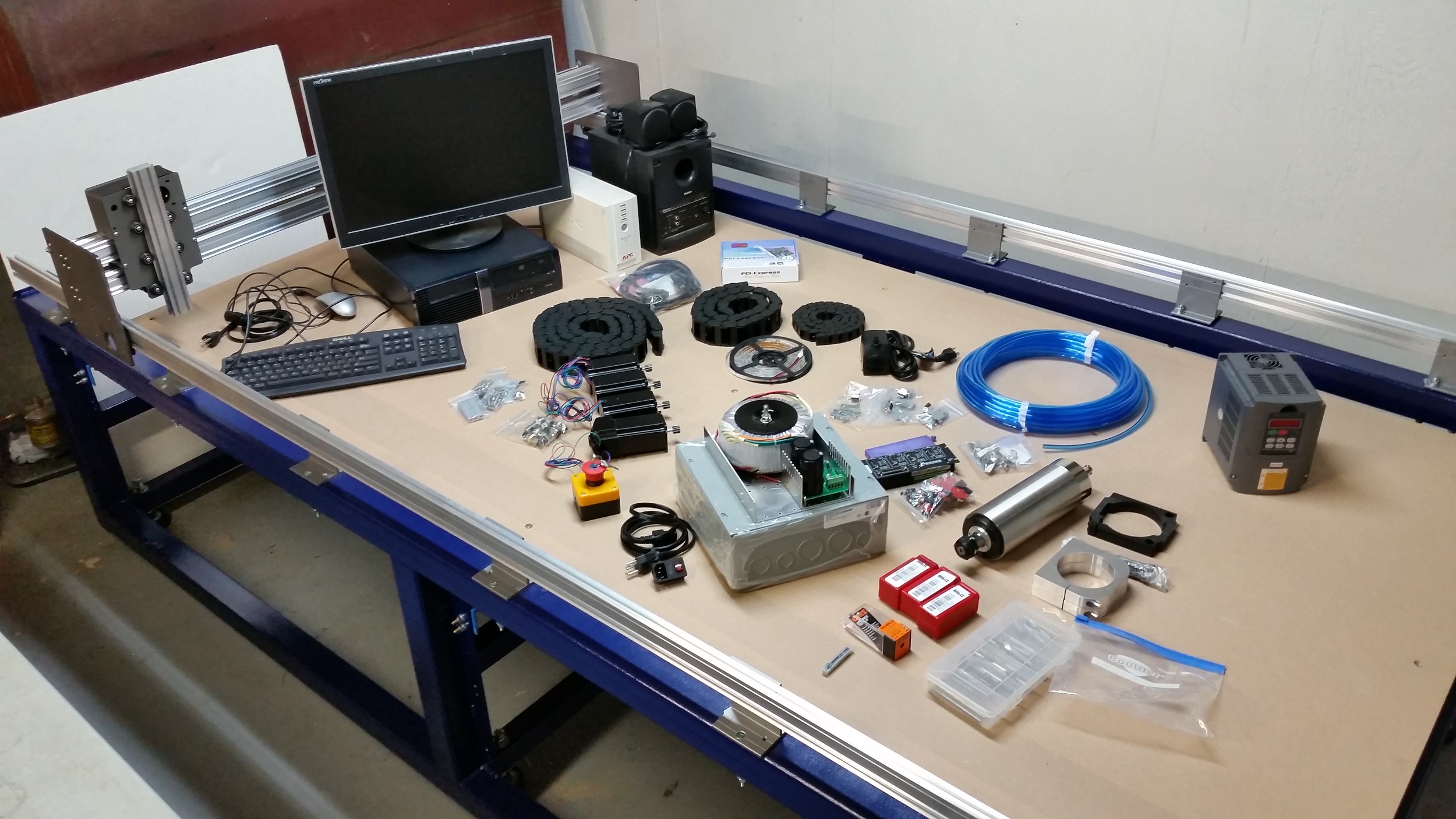
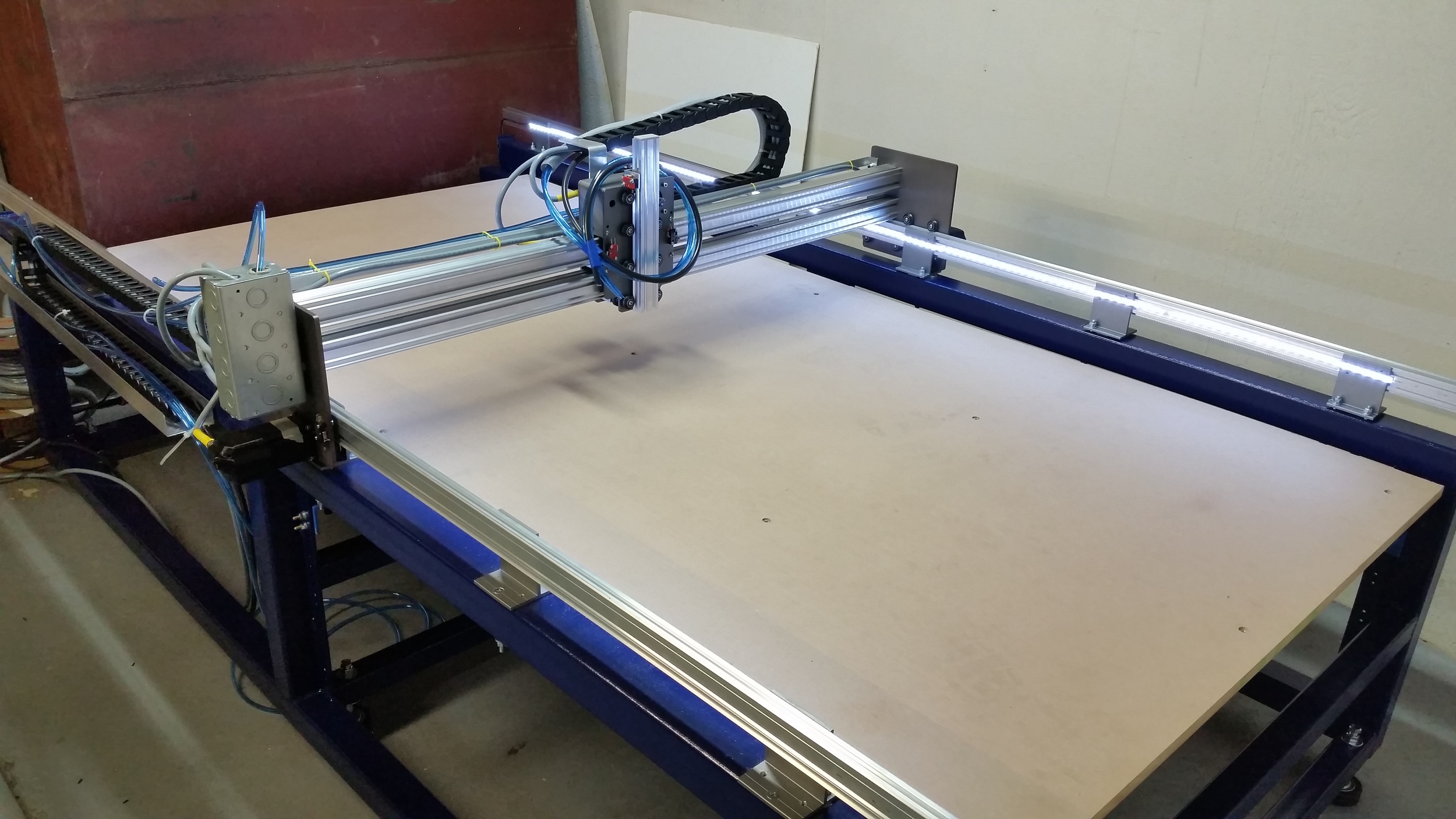
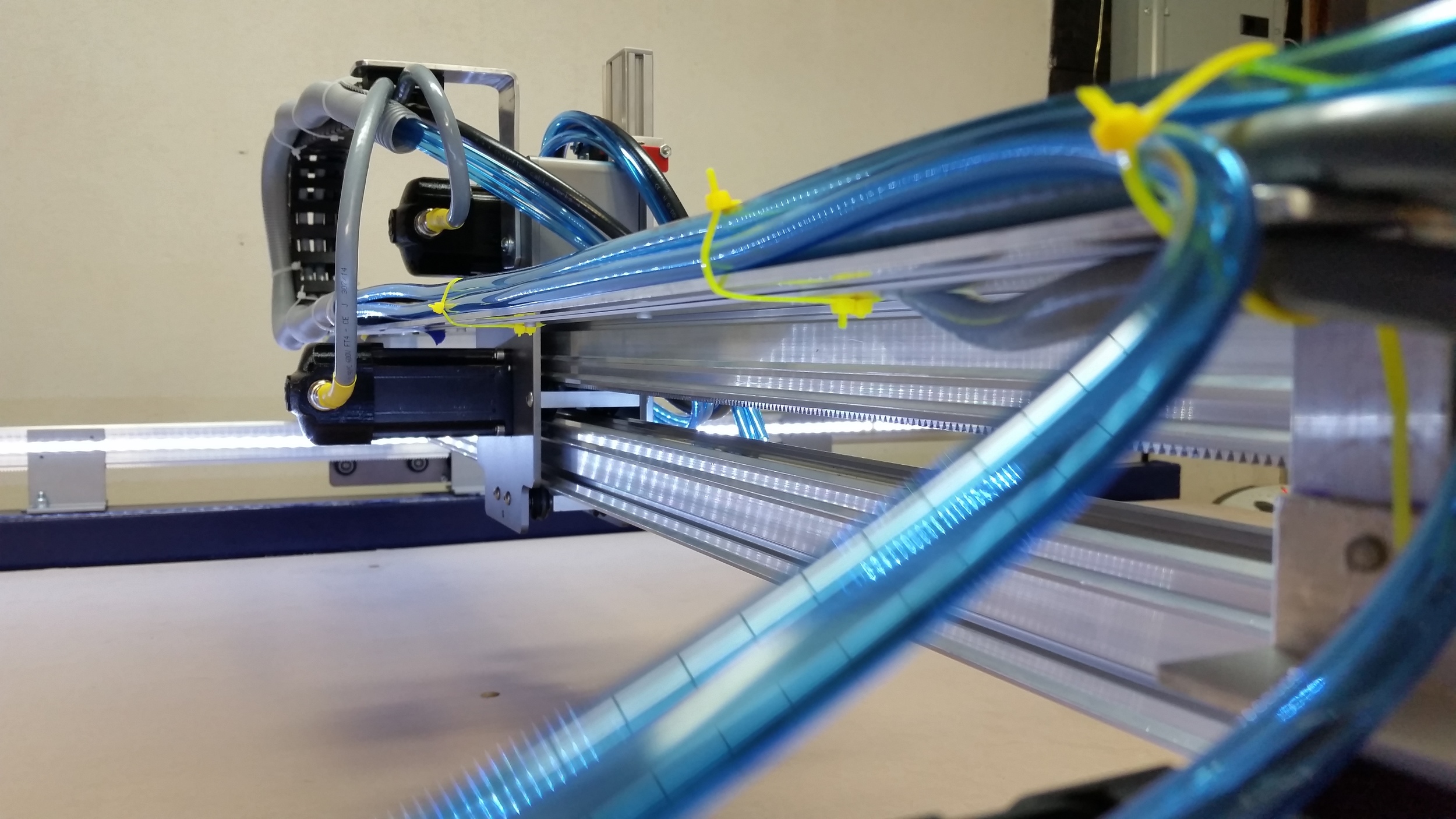
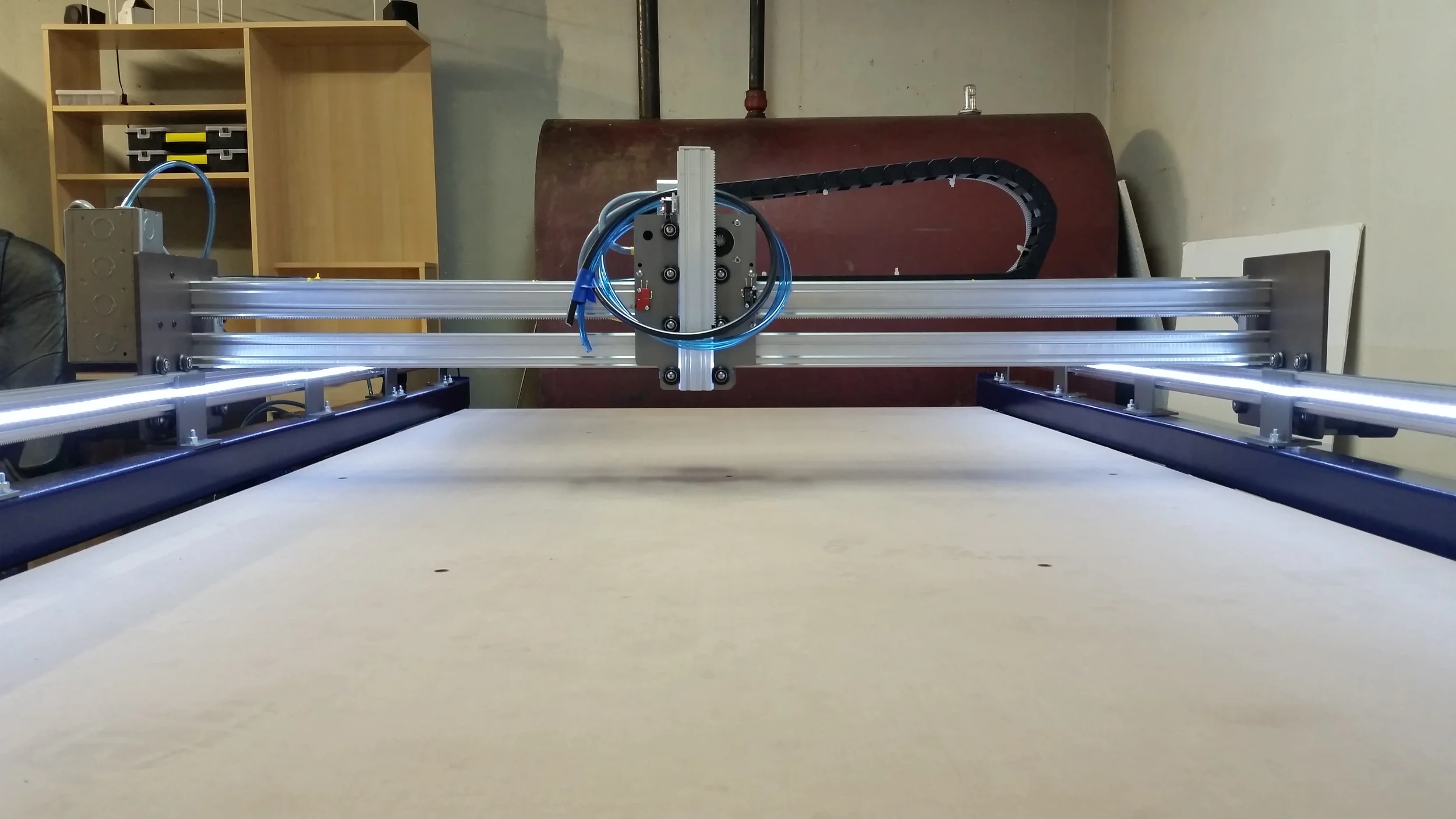
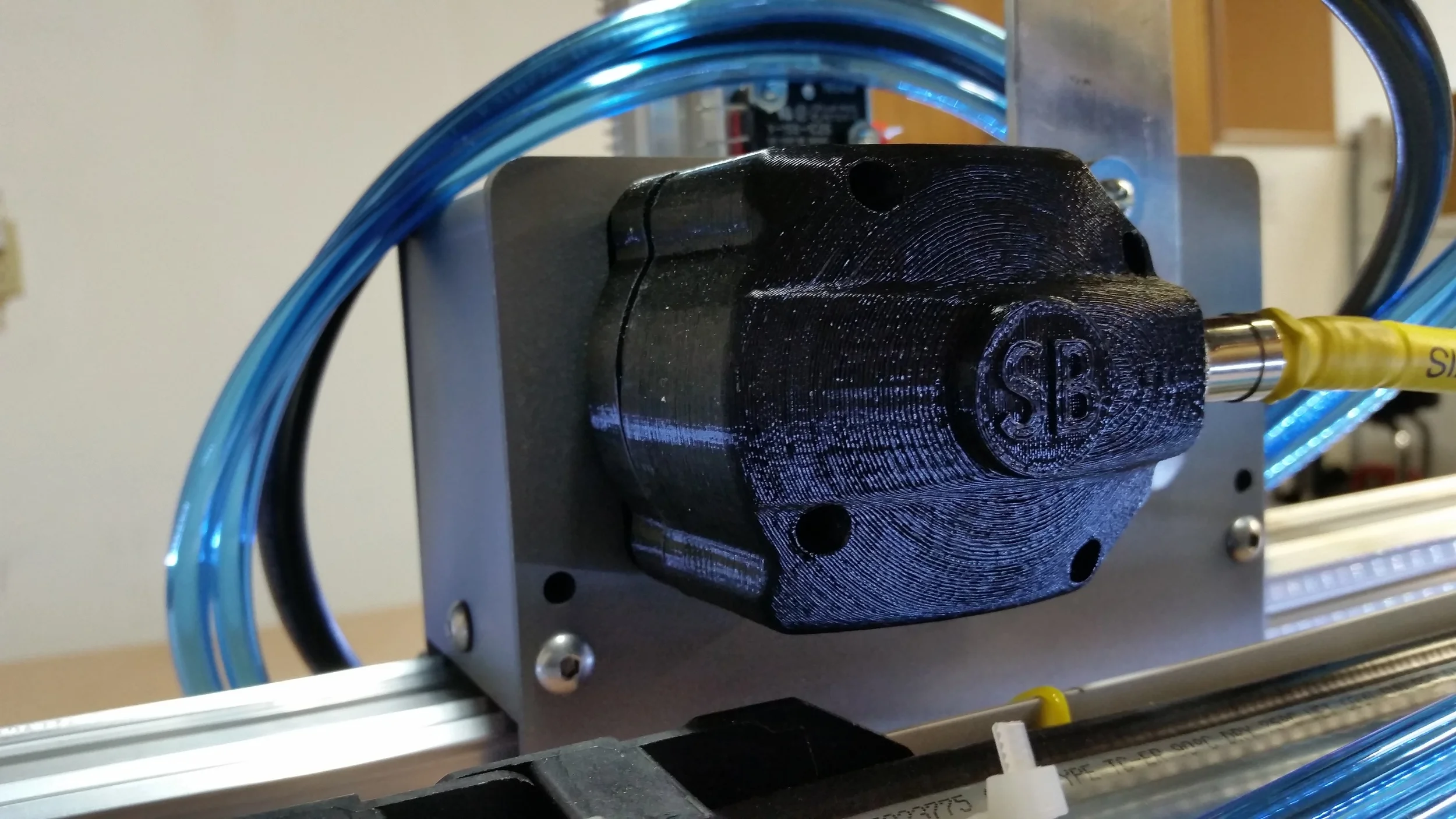
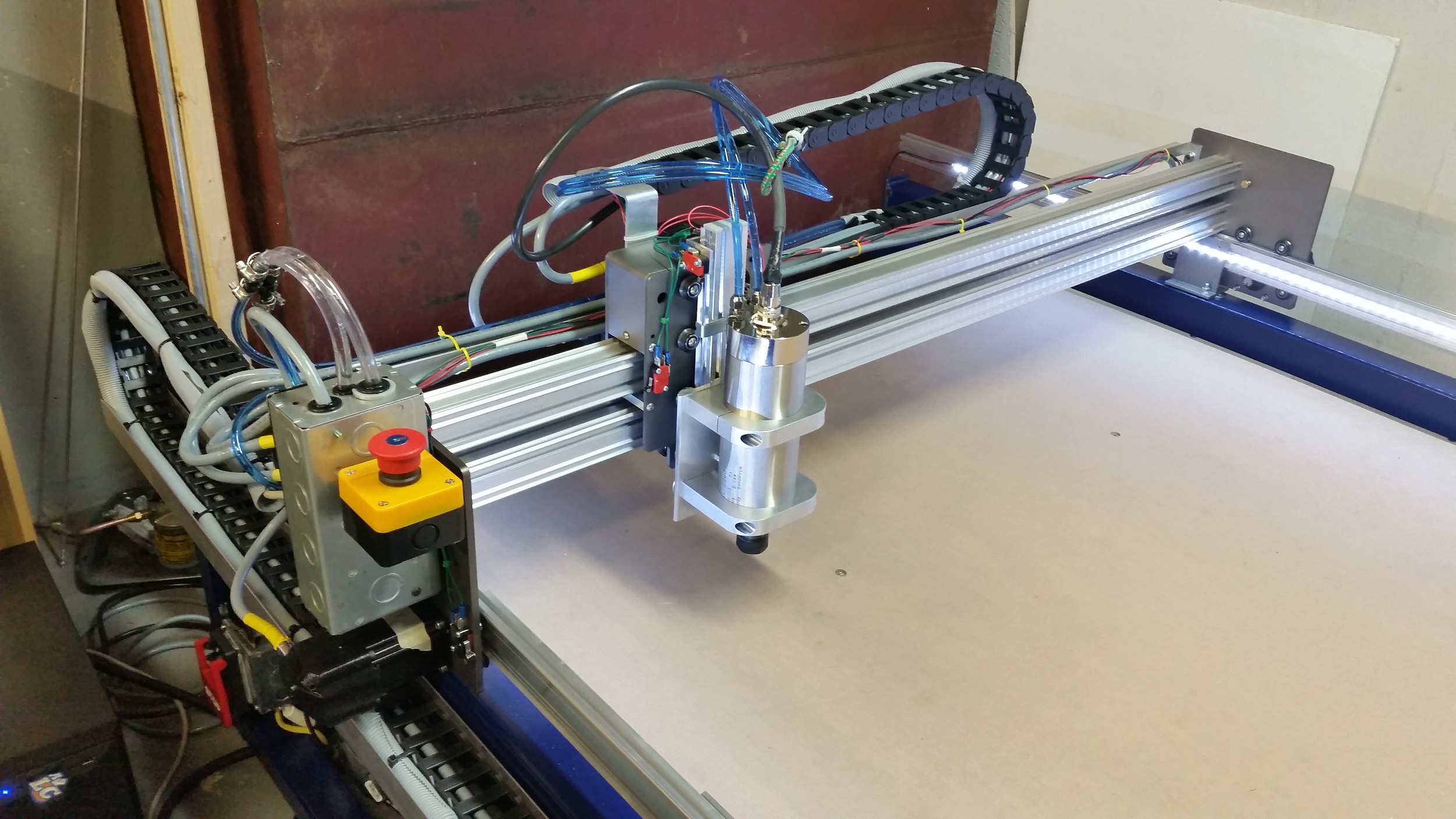
The machine structure is a combination of a motion rail kit and a custom steel frame. The steel frame was welded in-house with our TIG, and is designed to have an adjustable bed which can be raised and lowered as-needed to account for parts with significant Z requirements, or to be more rigid for sheet.
The rails kit is by a somewhat controversial make of CNCMogul. Many people have had issues with this make, but in our case it was a good fit.
It is a machine based on aluminum extrusions with v-groove rails called Makerslide, combined with some proprietary 'super Makerslide' which is equivalent to two sets of Makerslide stacked back to back. This design is not by most considerations heavy duty. It was however deemed suitable for cutting aluminum sheet, MDF, and hardwoods; all given appropriate feeds.
The machine is driven with NEMA 23 steppers (complete with custom 3D printed end-caps for cables) using a rack-and-pinion drive. The system is simple, suitably accurate, but has the potential
The spindle is 2.2kw water-cooled driven by a VFD. Water cooling passes from a reservoir through the Gecko 540 heatsink to spindle and then back. This beats the pants off a basic air-cooled router any day of the week and because this machine is in a basement shop and not an outbuilding, it's vital to keep sound sources to a minimum.
That doesn't mean there's no loud sounds: cutting through materials at high RPM brings some volume, and cutting wood/MDF predicates use of the 2HP dust collector which is quieter than a shop vacuum but only marginally so.
Using the Machine
Our machine does not use a Vacuum hold-down system, so we use the archaic method of using screws to hold our work material down to the table. By having the router pre-drill the holes, there's been no issues with cutters running through screws. It is more work, but since in most cases there need to be holes for fixturing later, it only adds the step of physically driving in the screws then removing them later. The method has worked well so far.
A few issues have arisen; control to the VFD is still manual, as the USB link does not seem to register. Current limit stops attached to the X axis rails limit the X travel, and a few other things mostly leading to small hits to organization and efficiency while figuring out the ideal setup.