What a Year!
Seasons Greetings! Thinking about what a year we have had and what is in store for us in 2022. We had no plan to go to SNF 2021 because Connecticut was restricting travel from Florida in February and March, then it was opened up and we went last minute. No one knew if SNF was going to be full or a flop. Turned out to be a great show - though we only had an engine to display. The airframe was too far along to disassemble and not far enough along to show off. Meeting the Hatz association members was awesome. We then had the big push to get the plane presentable and mostly done for Oshkosh. Oshkosh: Tornado and crazy stuff happening there and en-route. The huge response to the P-36 LiteFighter. Meeting the other Verner dealers and customers for the first time. Saw a real F6F Hellcat take-off and fly away as well as the Bally Bomber 1/3 scale B-17. Also met the family again and did a soft unveil of our 1/2 scale B-17 project. Really was an amazing week. Then there were major delays and work-arounds this fall and now we are finishing up strong. Expanded the team and our capabilities. We are getting excited to fly!
A little update on progress:
We finished the cowl flaps and are super happy with them. Gary and Trevor helped me make them and get them started and then Shin jumped in and worked super well on installation. Making and installing the flaps was way more tedious work than I had envisioned it would be. Of course, I’ve never built radial engine cowling flaps before. The current design is ground adjustable from fully closed to about 3/4 open. We can make adjustments during flight testing and can even modify them to open up full if needed. We can do better next time but these will be more than good enough for the prototype. Scott has designed an in-flight cockpit adjustable system. Learned some lessons that we will incorporate into the next one and other models. We added an exhaust manifold low-point drain. Radial engines can leak some oil into the exhaust when parked. Steve Wolf showed us how to do it and we were limited in available real estate - so improvised from his design. Gary is an amateur small engine repair person and suggested a chain saw compression release valve instead of a Curtiss drain. Will report on how that works out, but looks like it will be perfect. Fire-proofed the firewall penetrations. Added a ton of nut plates for the cowling and access panels. Added the gun blisters to the cowling and I am considering adding the ADSB-IN/WAAS GPS all-in-one antenna (Uavionix EchoUAT with SKYFYX) inside the right (starboard) blister. Will need a ground plane under it - so will put foil sheet on the inside of the cowling up there. Should fit and would have good all around coverage. The ADSB-out antenna will go on the belly. Shin and Scott added the pitot mast to the left (port) wing tip. Love the look and detail. Scott had 3D printed the mast head and the rest is aluminum. Scott is still making landing gear parts on the Mill and lathe. Will be working on the landing gear legs for the next couple of weeks.
Electric Boat (General Dynamics) is gracious enough to shut down the plant, yards and design/engineering for the last week of the year (without pay). We call it “Shut Down”. Novel I know. Well, everyone at EB has been super ready for “shut down” and are in “Shut Down mode”. Most EB folks take it easy for the week. WE are gonna spend a long hard week in the shop working on the punch list and finishing everything up on the plane. Will likely run the engine again during the week if the New England weather cooperates. I am designing a boot cowl heat shield and some cylinder baffling, map box and arm rest for the cockpit and will get that stuff installed. The landing gear may not get finished till the first week of January. It just is going to take what it takes. The fixturing takes a lot of time to develop. As soon as we can, we will make some video of the P-36 to post on our YouTube channel and our web site. Stay tuned! Have a great holiday and New Year! - Stay Safe!


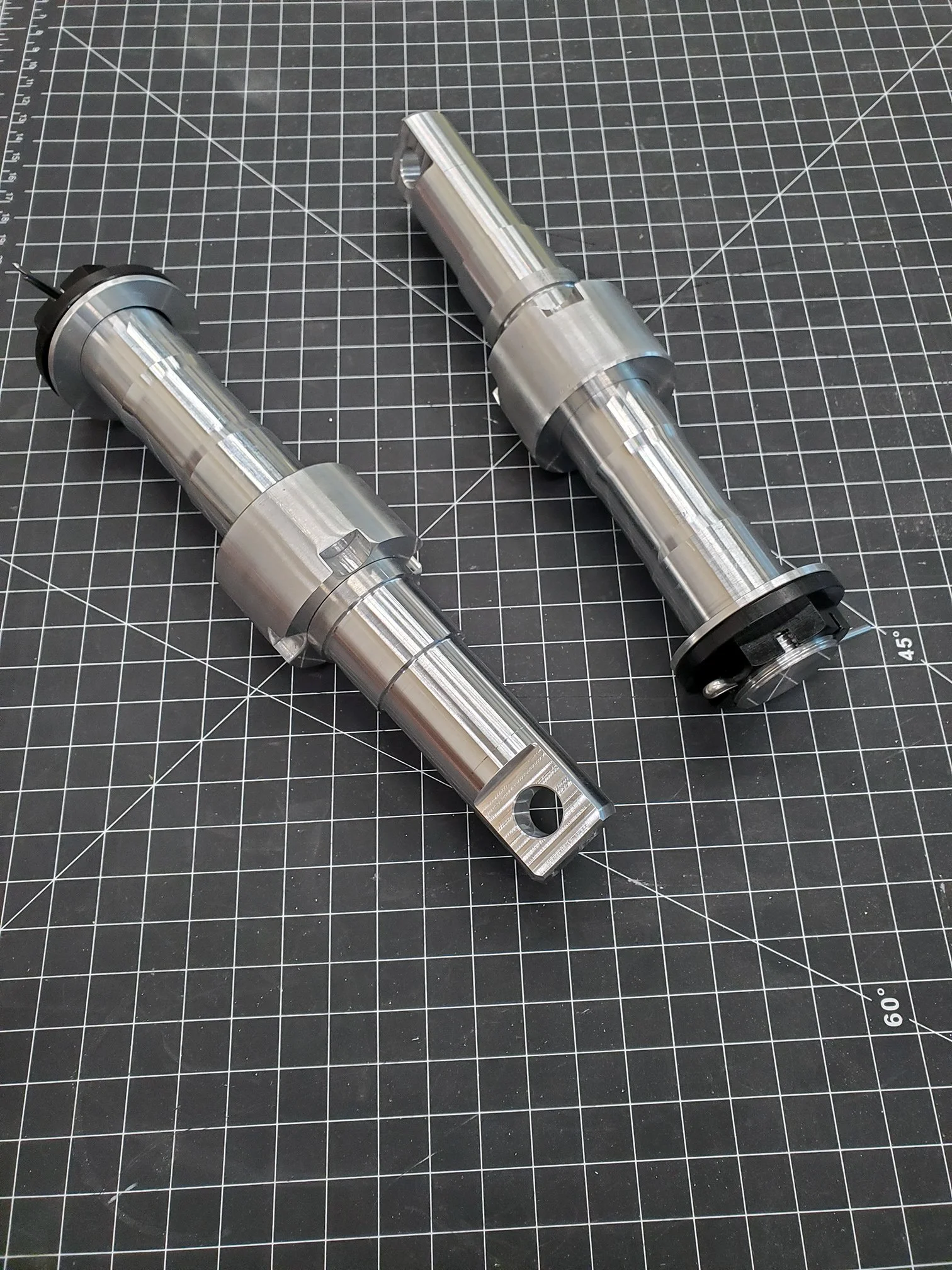


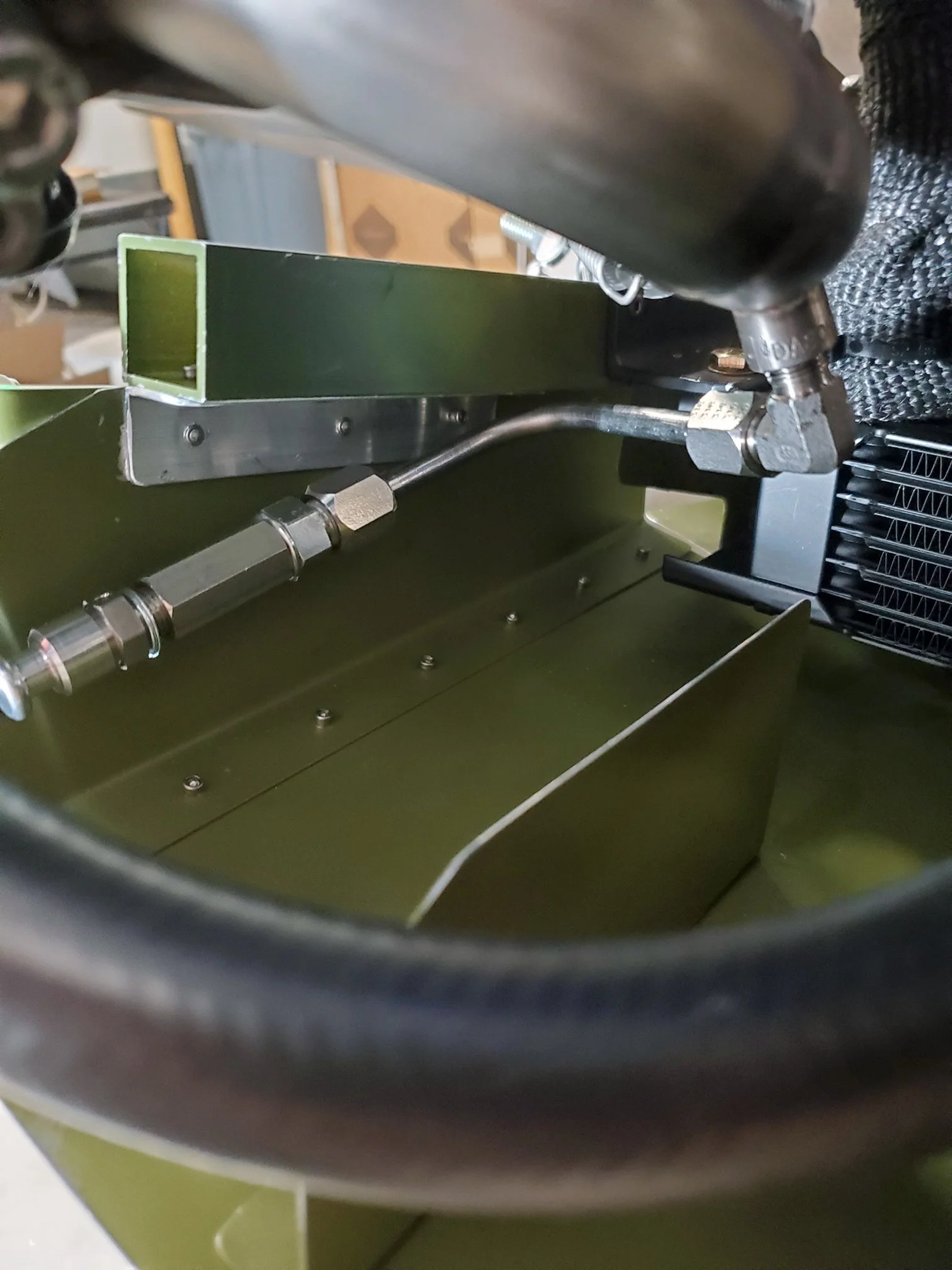

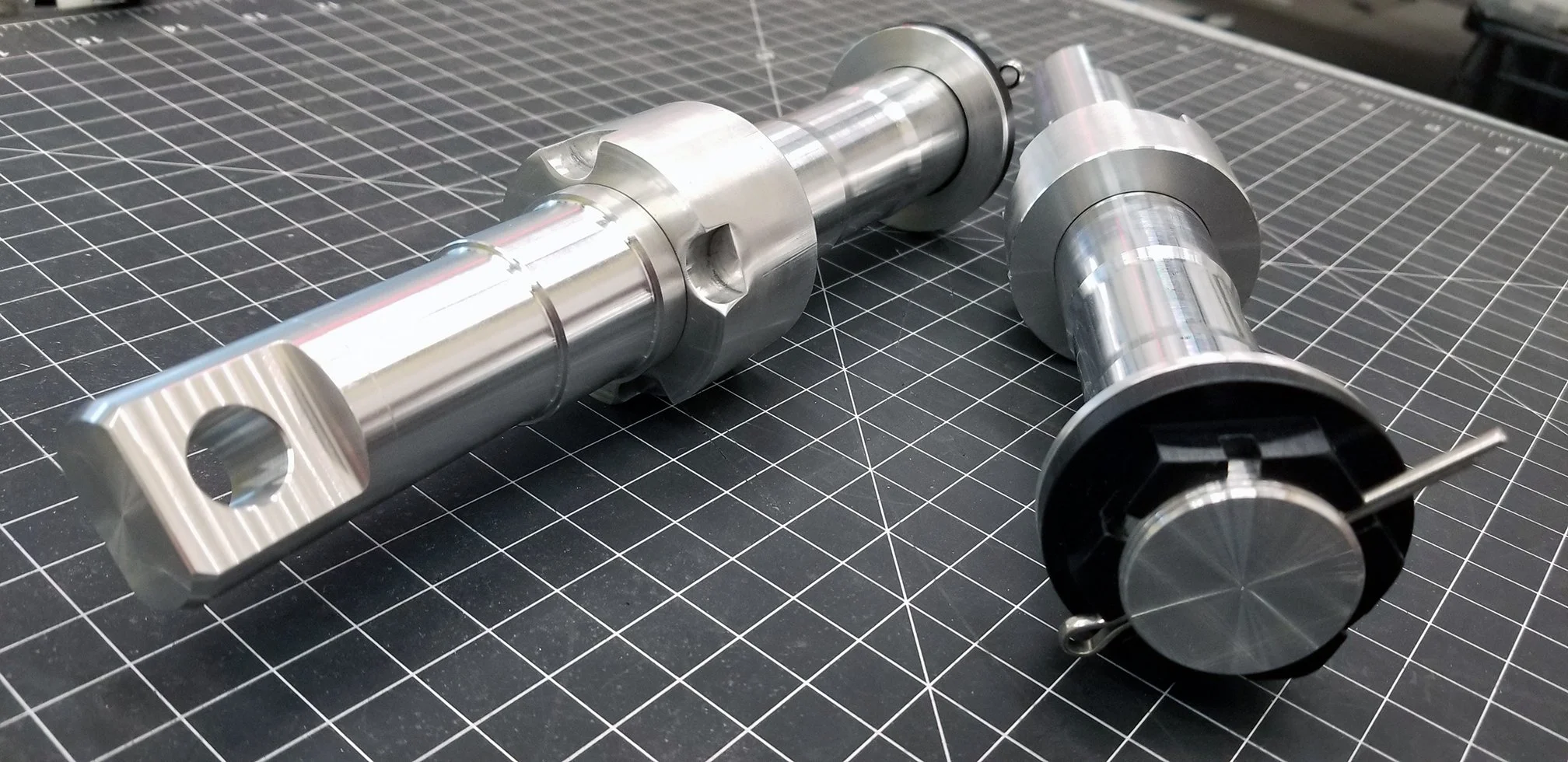
