Oh Shoot!
Been an eventful month of October 2022. We have been flight testing and working on temporary wheel pants and leg fairings in order to speed her up on cruise. That required attachment brackets to be fabricated and fitted to gear that were not designed for pants. We need to find out if the wing is good for stalls and for high cruise speeds in order to develop the Beta/kit version. We just need a few more flights to get that information. We need to determine if wing area, washout, stall behavior are good or need refinement. We have been fighting high engine temps which has kept us slower and lower. The cooler weather now is lowering the engine temps a little. We will get her to altitude and try some stalls and dives to check the control forces and behavior. Before doing that, I needed to get some spin training.
As mentioned before, we skipped adding flaps to the prototype. That was a mistake as landing and approaches are not a fun experience - cant see the runway over the nose. I have been holding it high for the lift needed from the slower wing, or it drops like a rock. So power and nose high attitude. I was discussing this with Steve Wolf and he was saying there are several non-standard approaches that he could show me that will help keep the runway in sight and allow for the higher angle of attack. Round engine tail-draggers have to be flown differently than a Cherokee. I took him up on it and booked a flight to Florida. Awesome trip and I am super grateful for that instruction! One of the best weekends I’ve ever had! Camaro convertible, perfect weather, some flying with an expert, hanging out with aviation friends and seeing their projects. Great food, great beer. Hard to beat!
I got back home and back to the landing gear project. The mounting brackets were not fitting correctly. The angle needed to be changed - requiring they be cut and re-welded. So instead of mounting the wheel pants, took her up for a flight to get back in the groove. We had borrowed an Ilevel BOM unit from a friend and had mounted it on the wing. Planning to get some data over the next few flights to calibrate our pitot sytem in flight. Kept the cowl flaps closed and she was climbing out at 1400 fpm at 90 mph. Started getting close to temp limit and I lowered the nose and power. Cruise climbed at 100 and the Verner’s 2000 recommended maximum continuous rpm. Got her up to 2500 feet and cruised around the airport area at different speeds and rpm settings. Did some turns and banks, dives and climbs. Was having a fun flight. She really is going to be a fun machine when we have the heat and speed issues fixed. Alas, fuel getting lower, I decided to bring her in for a landing.
Well I was a lot more at ease with the landing after Steve showed me the approaches. I chose the diving one where you stay high and dive toward the numbers and then transition to flying a few feet above the runway bleeding off speed. Well, I messed up and got her a bit too fast in the dive and was pretty fast over the numbers. Bled the speed off over the runway - its 4000 ft long so not an issue - and then bounced it, corrected and stuck the wheel landing by pushing the stick fwd. She jerked a little but other than that it rolled out straight and the engine idled along just fine. Parked at the hangar and got out. Gary was pointing at the right wheel. Bent the right lower landing gear leg and clipped the very tips of the propeller. Oh Shoot! Plus words I can’t repeat here. Didn’t seem that bad (I’m actually lucky the leg bent and didn’t break - that would have been bad). The landing didn’t seem any worse than previous bounces and I never felt the prop hit. I did raise the tail - maybe a bit too much but didn’t feel the prop hit. Well the plane is sitting there in the hangar. Still looks great - just don’t look at the wheels. Even the prop looks fine - just don’t look at the tips. All in all, lucky. It was all my fault and I should have gone around and planned the approach better.
Guessing that the extra speed added to the forces applied to the axles and our stainless steel lower leg wall thickness was insufficient. Found the weak spot! The lower leg on the Curtiss is a full cantilever unlike a Mustang where the wheel is directly under the strut. Currently, the right tire is tilting toward the gear leg about 20 degrees and almost rubbing the leg. Looks like it did rub it for a revolution or two. The left lower strut is just starting to deform - slight hint of it. But looks normal. The rest of the landing gear is fine, straight and un-damaged. The yellow tips of our NR Prop are abraded down about 3/8 from the very tip - they are rounded and so just a little material is gone - but being carbon fiber blades - they are toast. The engine will be fine - but we will pull the prop and check the hub for concentricity and square to centerline, if within tolerance and fine - will re-torque the hub bolt onto the crank-shaft. When it happened, I was trying to slow down - the engine was at idle and the prop was wind-milling. The Verner radial is very robust. She was running fine after the strike so the split crank didn’t get spun. We will have to do some ground runs and verify integrity once we get a new propeller.
Ah. A new propeller. Well the existing one was likely not the right prop for our airframe. We knew pretty quickly that it wasn’t perfect. Ideally we need an inflight adjustable to get a higher cruise speed and good climb. Also, after discussing propellers and reading everything we can find about selecting propellers, we are thinking a good part of our issues with landing and approach may be due to the propeller being a huge air-brake. A gentleman graphed various speeds and blade angles on his Zenith 750 Cruiser and found that higher blade angles caused excessive sink rate (sounds familiar) and terrible flare on landing (sounds familiar). He also plotted a 50 mph difference in 5 degrees of blade angle. This may be one reason we are much slower than expected. The wrong prop. We have a bit too much diameter and who knows if the twist in the blades has any efficiency for our speed range. We really need a purpose designed propeller from someone we can communicate with.
We are not getting responses from NR Prop - they are at war and out of power. So we have been contacting a number of propeller manufacturers. Most of the Worlds prop makers are 3 to 9 months out for delivery. Yikes! We can’t sit here for that long! We may try a fixed-pitch, 2-blade wood prop specifically designed for our flight envelope, diameter and rpm for a datum for comparison with other propellers. GSC in Canada can carve one in 10 work days. Sure, it won’t look right, but its for testing only. We want to see if it has less vibrations and runs smoother as well as the performance range. Ultimately, we want an electric three blade WW2 looking prop for the Verner as well as the other engines that will be used in the P-40. We are looking - most of the manufacturers will not supply their ground adjustable or in-flight adjustable props for Verner or other direct-drive engines. Some do and we are finding out who and what the difference is that allows it.
So we are down for a while. Likely the winter. The flying season is quickly wrapping-up here in New England - as the days will be cold and windy most of the time. During this time, we are going to mod the wing and add half-span split flaps. Scott and I are designing those right now. We will fix the landing gear and are deciding if just making new thicker walled lower leg struts or if we switch to the planned oleo gear legs and get rid of the springs. We also discussed with our engineers about re-making the wing center section to add wheel wells, flaps and 10sf of wing area or if we need to make new outboard wings with less washout twist. This all is doable, but takes more and more time. We have decided to fly her first with just adding flaps and maybe oleo landing gear legs. Might eliminate or reduce the bouncy landings. Then, get more data with this wing and then decide if further, incremental mods are required on this machine. Ideally, we want to start work on the Beta airframe asap. This delay is also a delay to our planned production start of the Beta kits. I will keep you up to date.
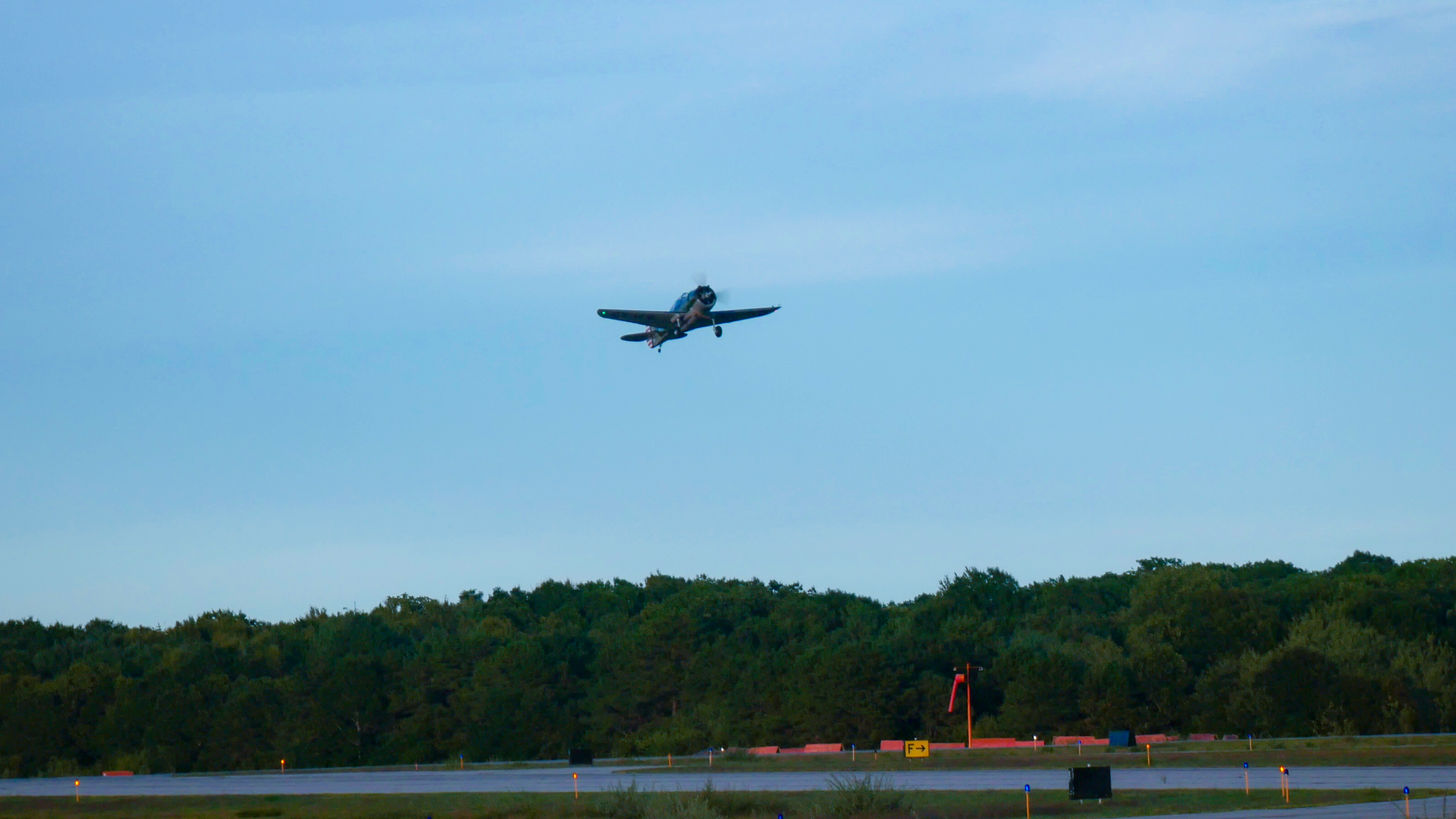
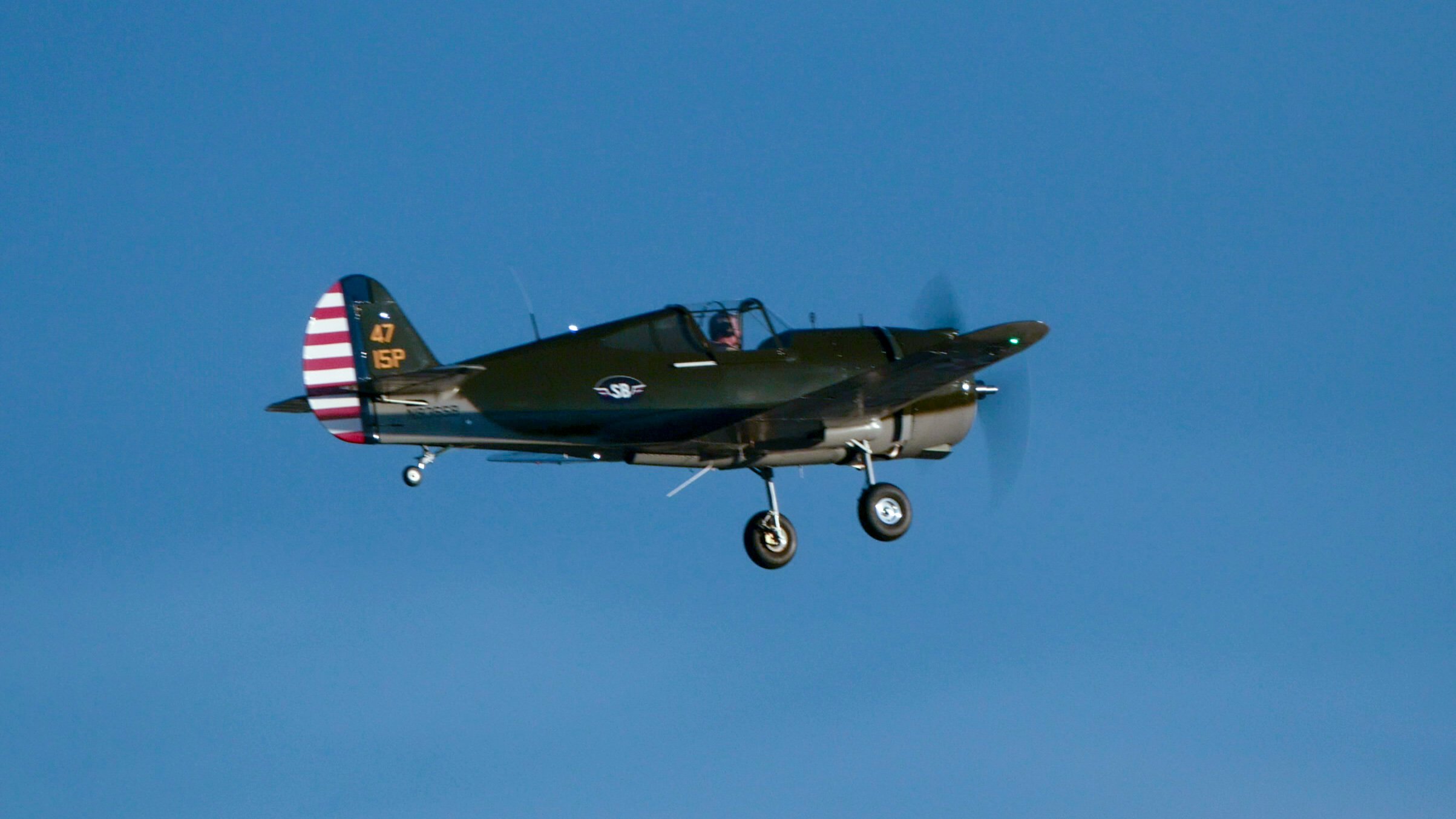
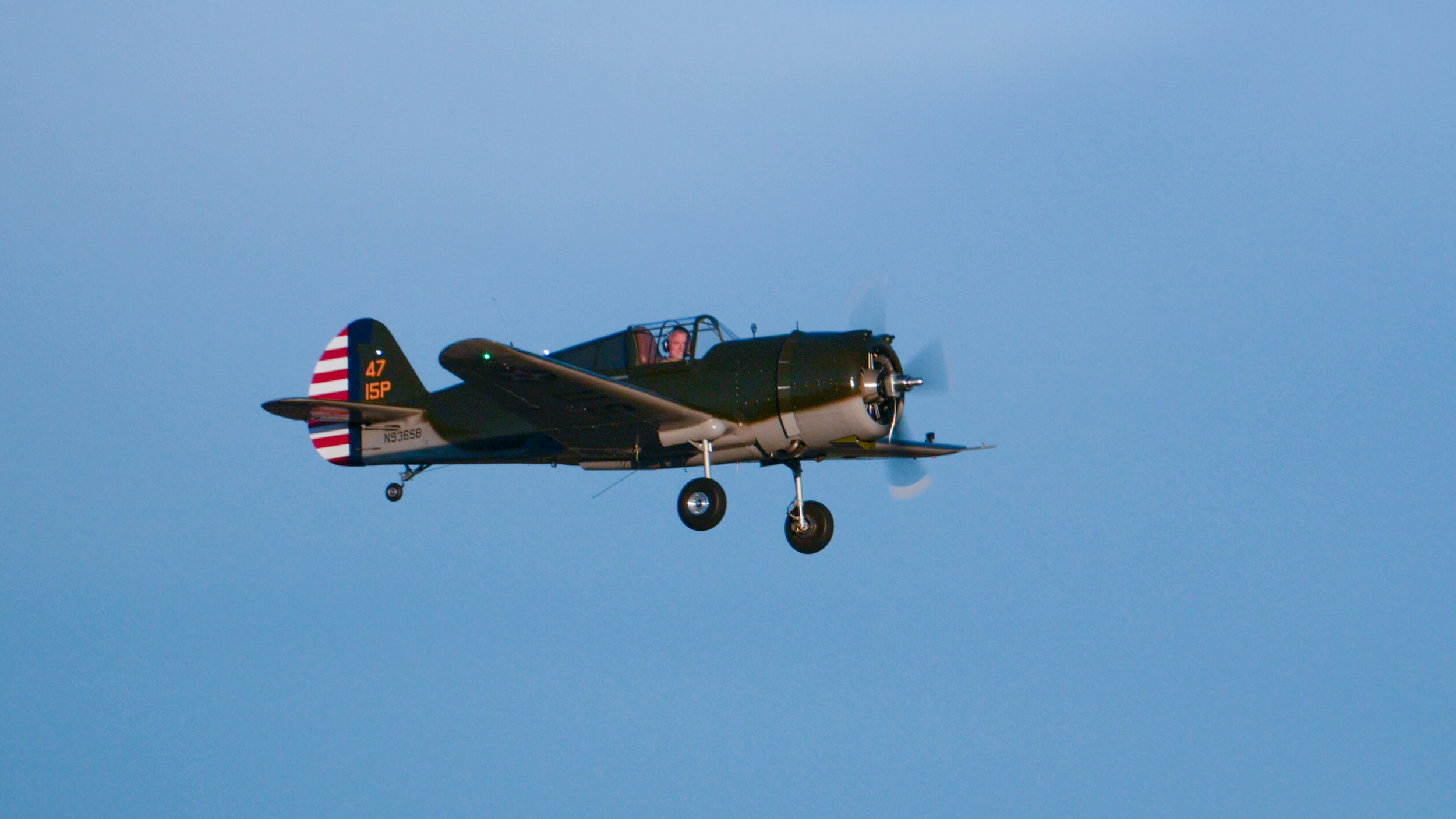
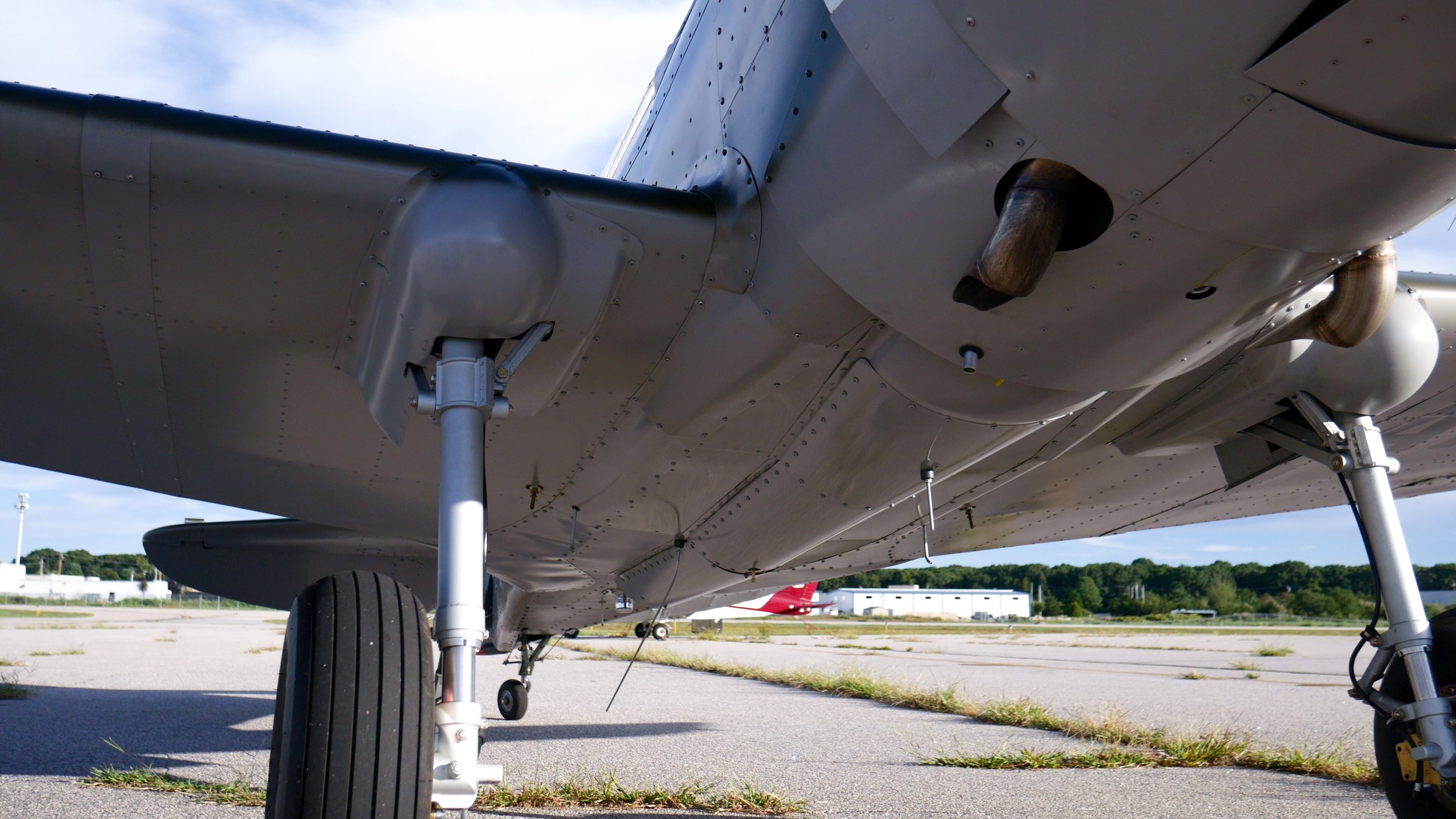
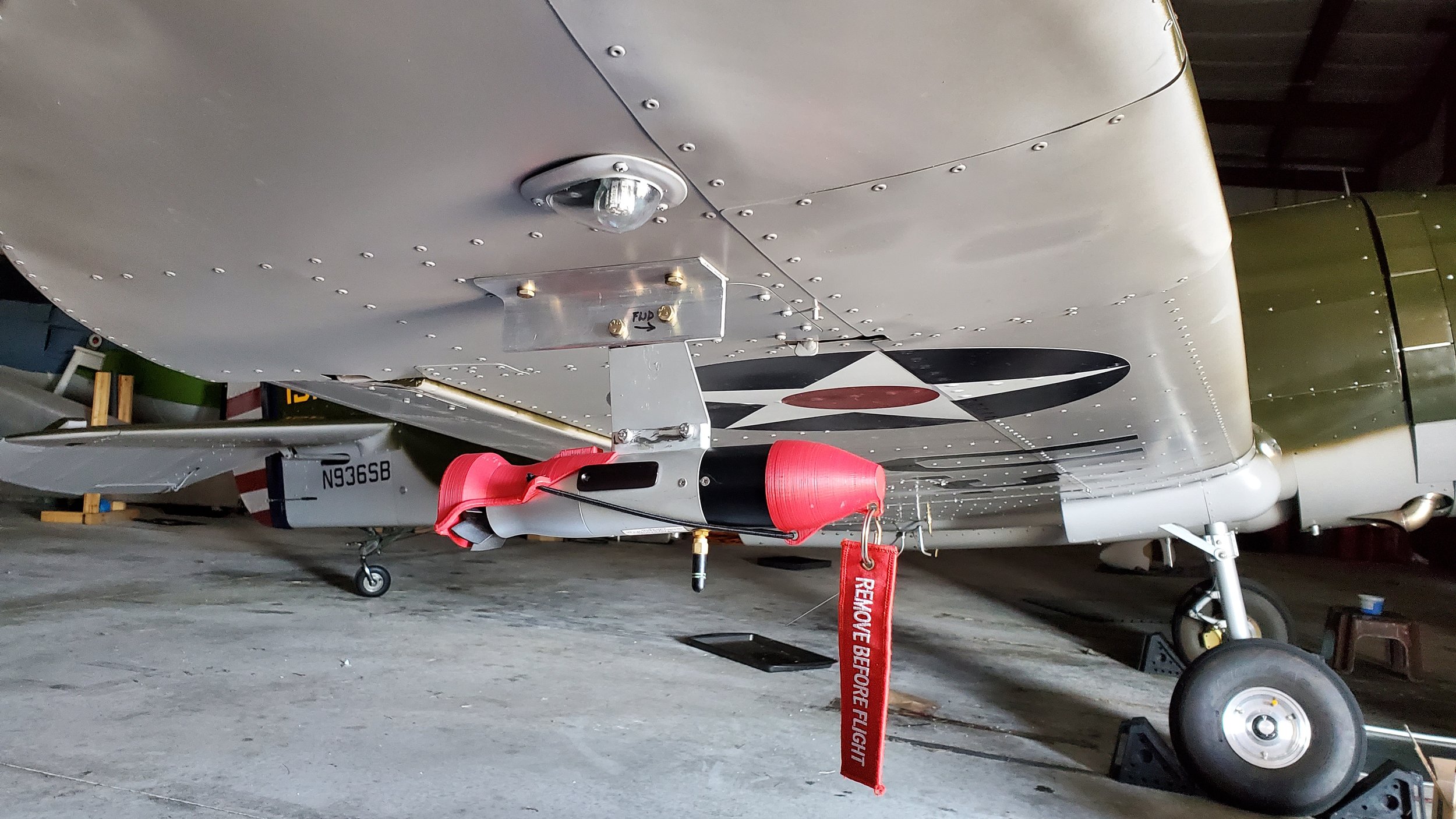
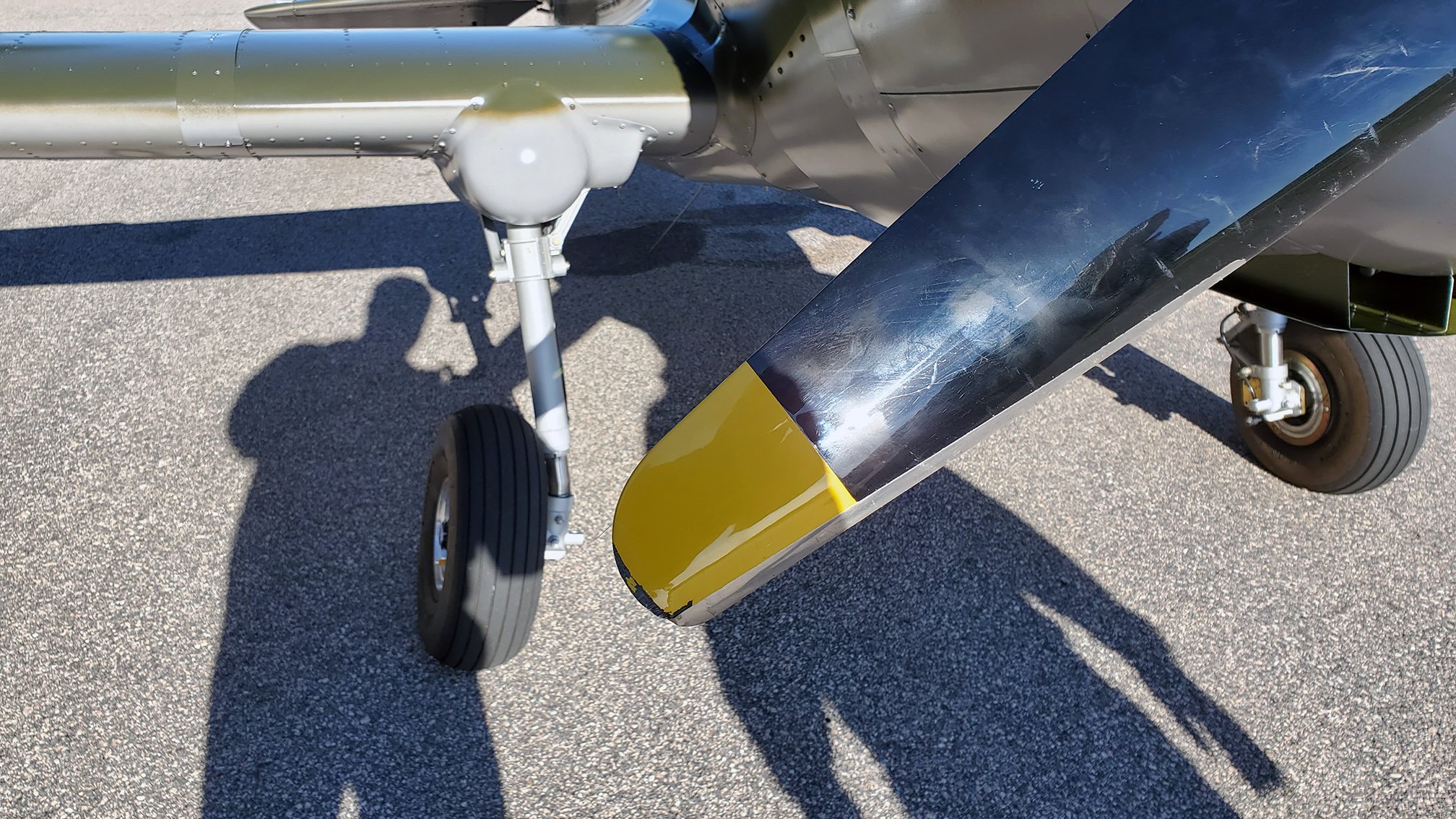
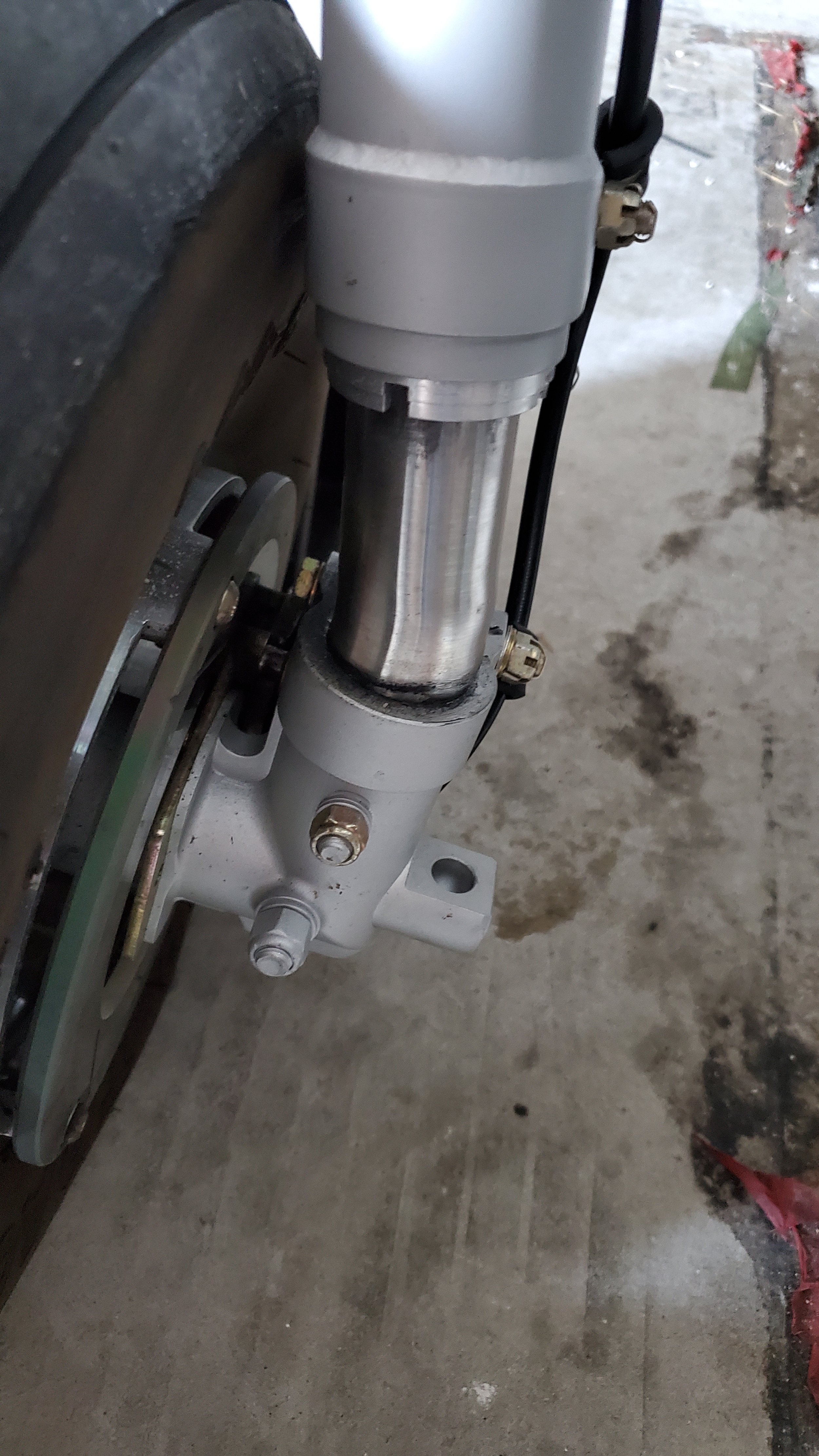