Taking Shape
Been making parts fast and furiously for the Lite Fighters. We added the bulkheads to the P-40 frame and have been working on all the internal components. Again, as we are making all these parts we are making two sets. So the F6F will mostly be installation work. We only have so much space so we are concentrating on the P-40 first. Controls, baggage compartment, rudder pedal assemblies, tail wheel assembly and mounts, etc... It will get the Rotax 912 and we have a friend with a brand new - but 15 year old 80 hp engine we can install - after we get it torn-down and all the rubber parts replaced. The design will handle any of the 900 series Rotax motors - well, the new 915 may need to be engineered as the inter-cooler sticks back too far. Anyway, the 80hp will match-up with the F6F and the Verner 83 hp 5 cylinder we are ordering soon. It will be interesting to compare the two for performance.
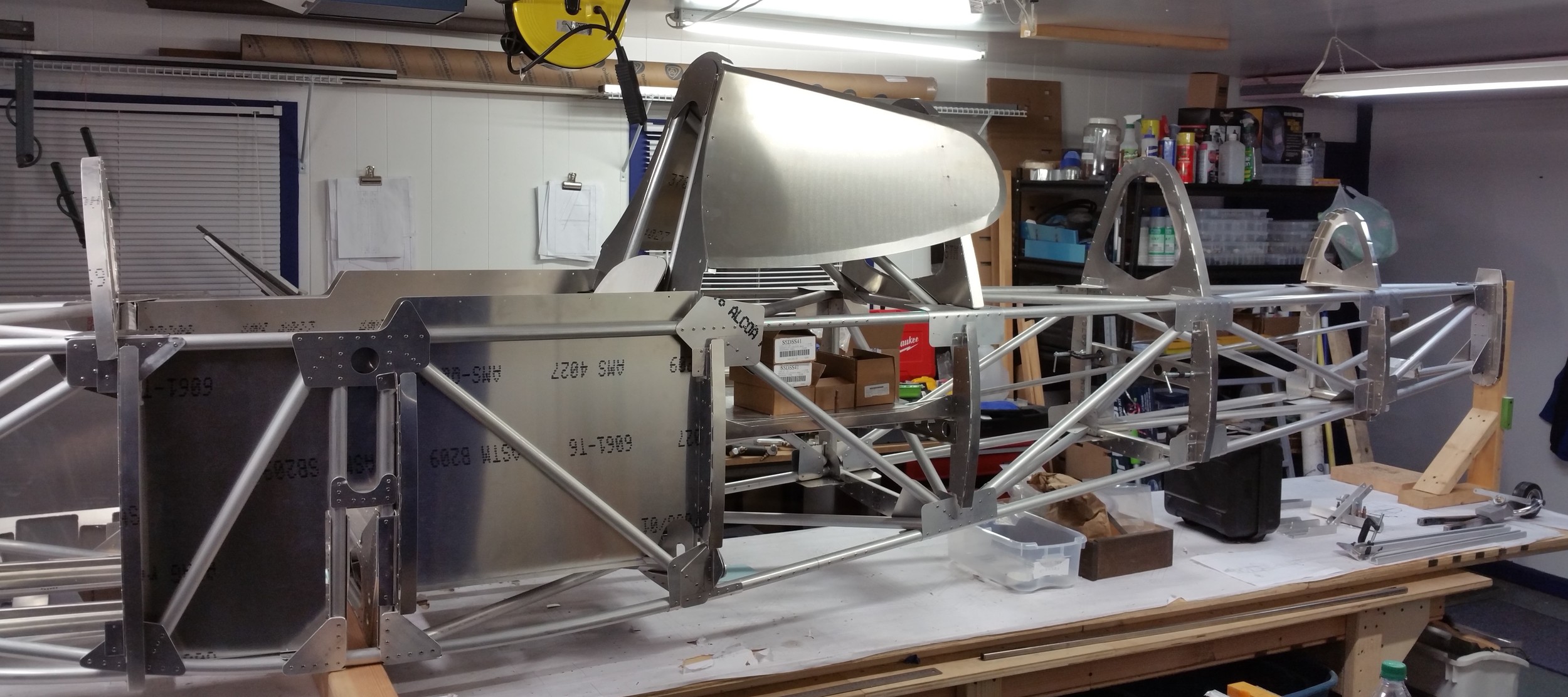
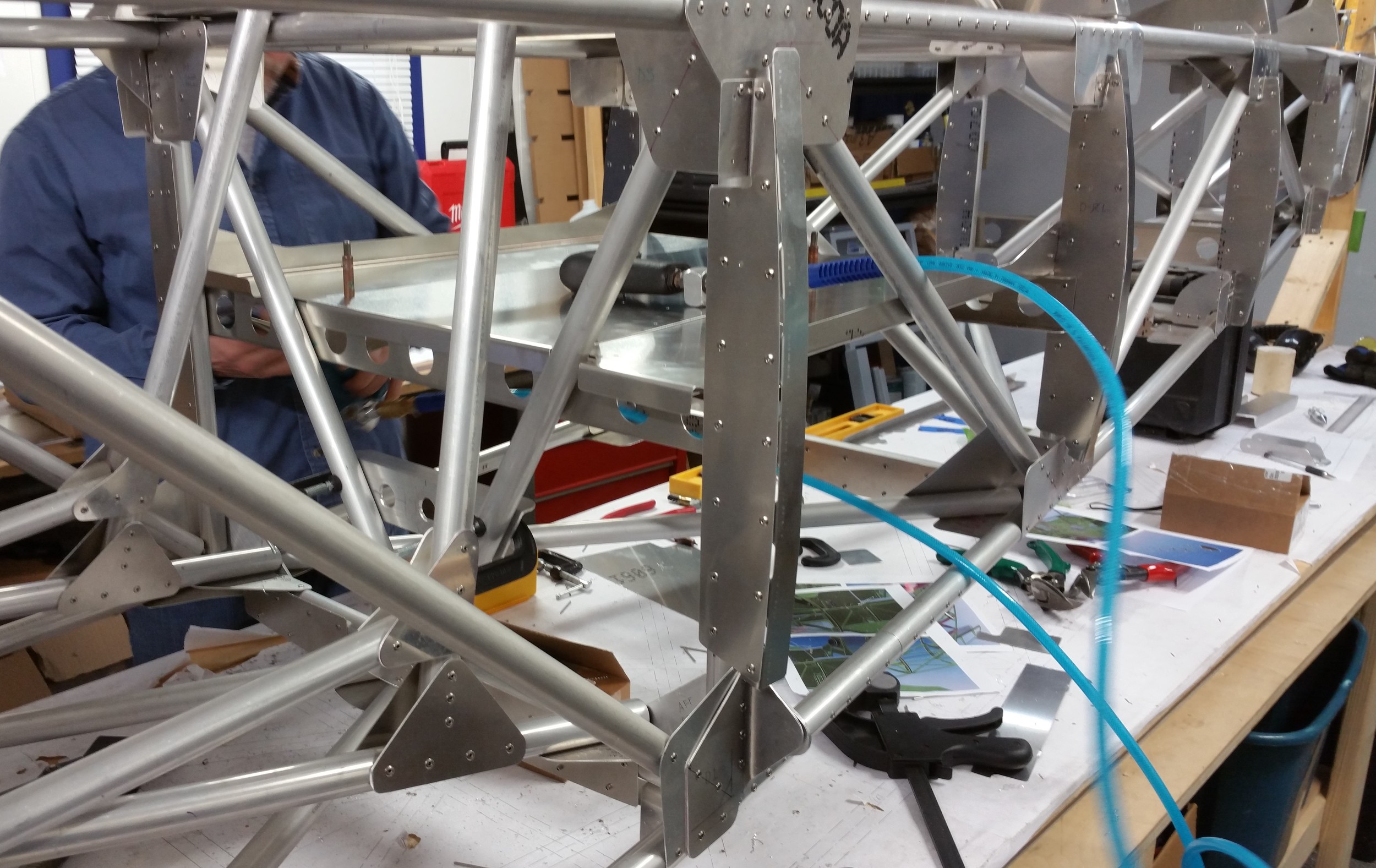
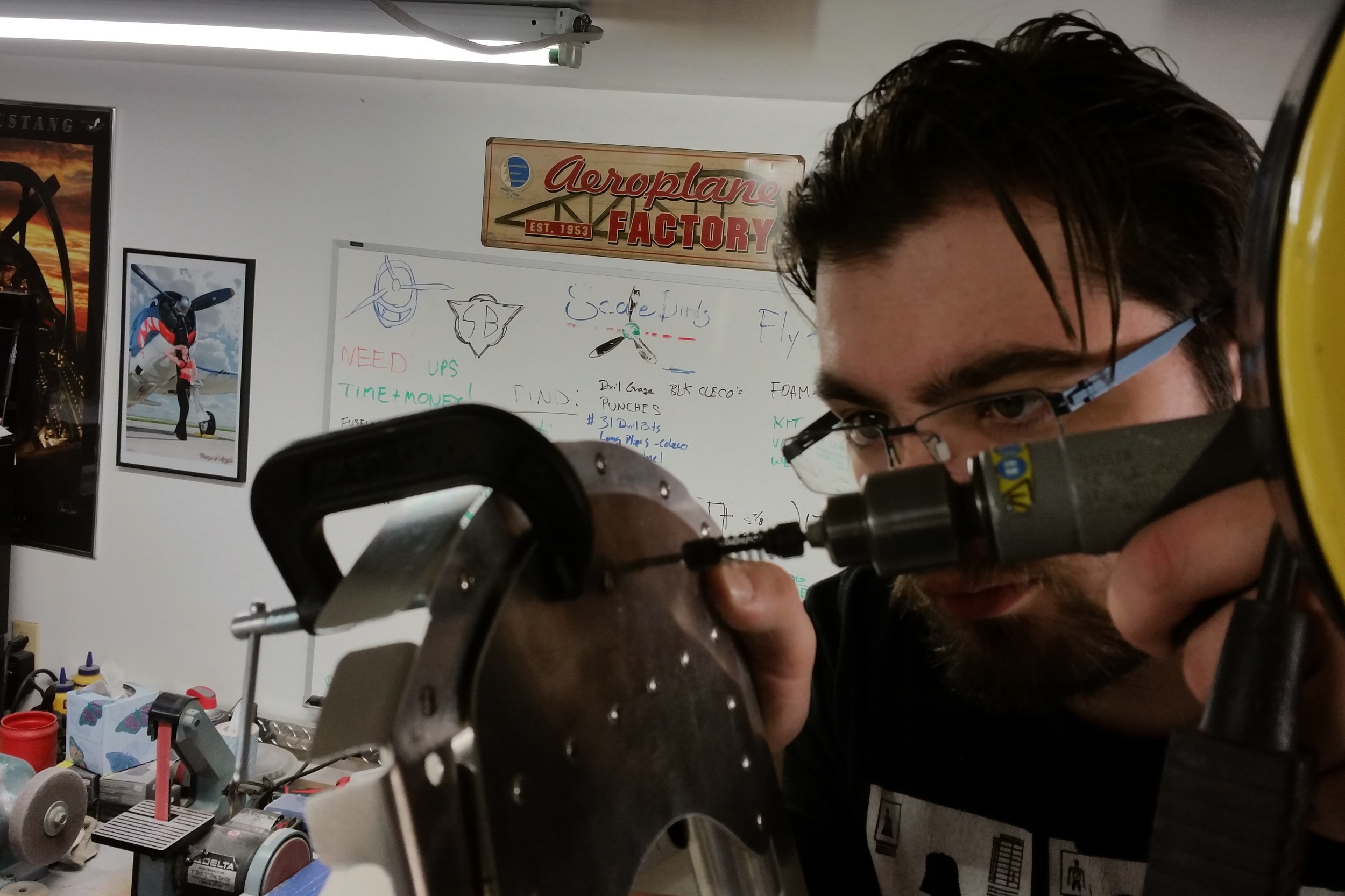
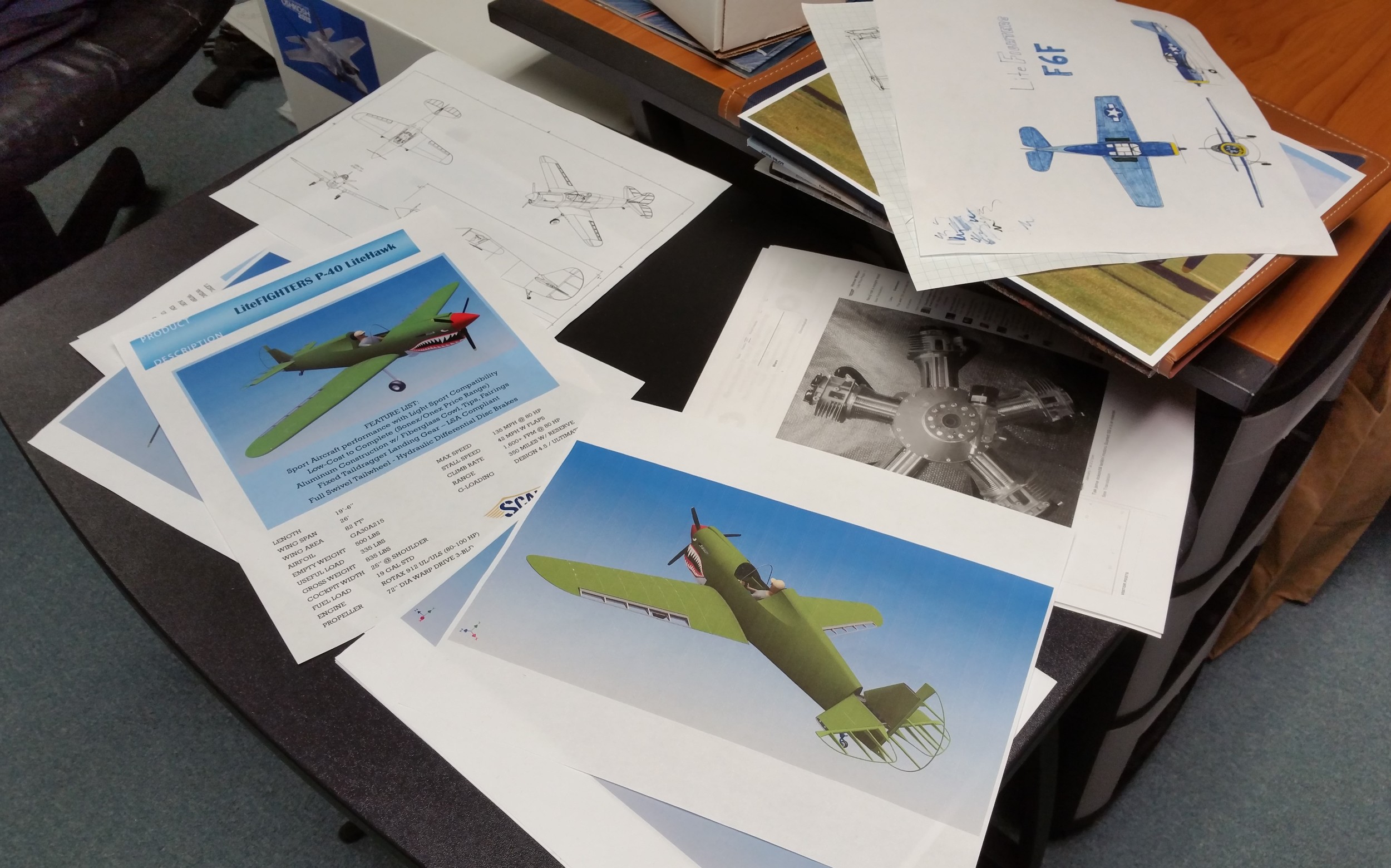
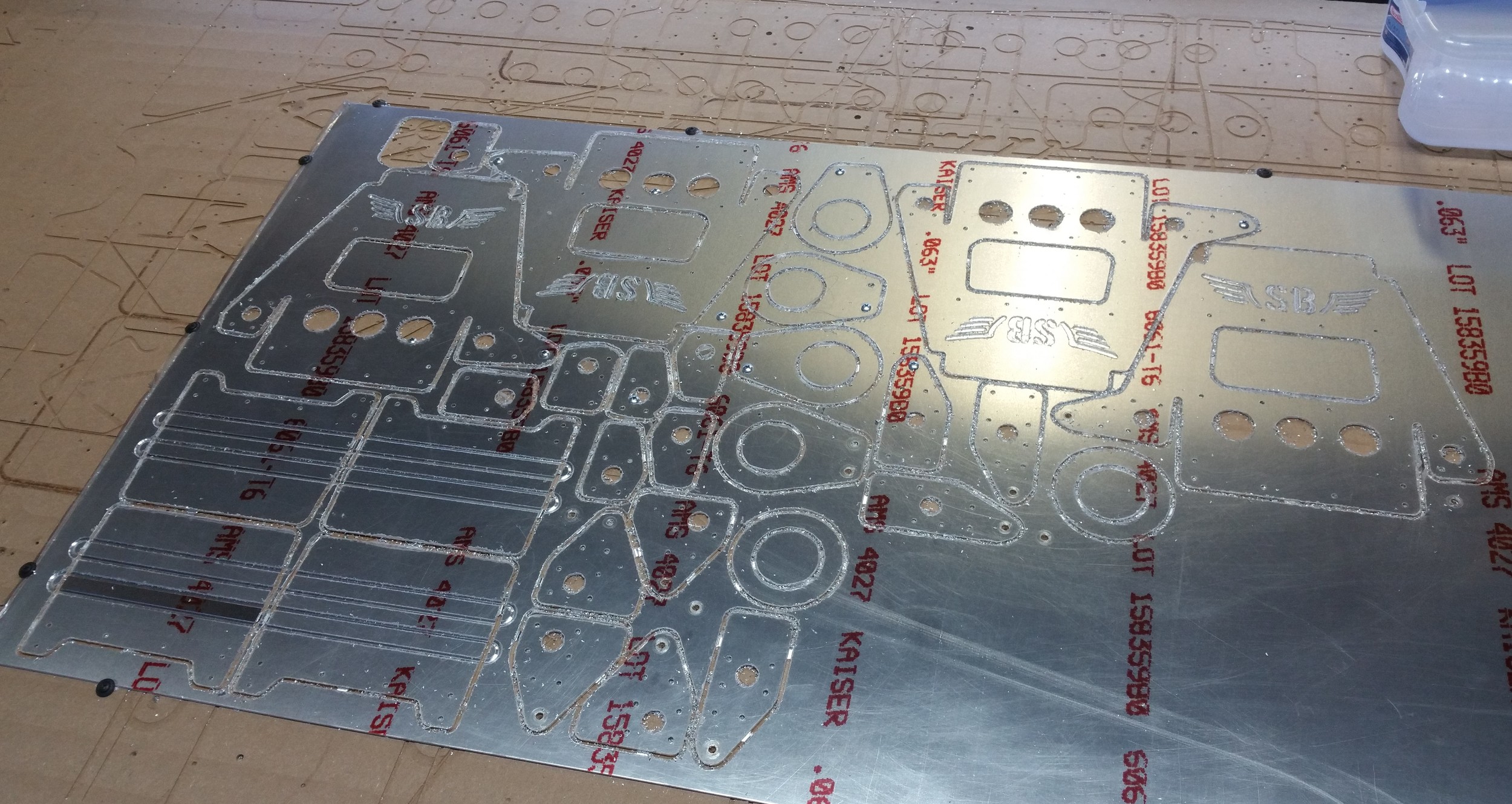
Speaking of performance, we are seeing some very remarkable preliminary numbers. Flight testing will certainly tell the tail, and I don't want to be too optimistic. Lets just say that the P-40 will climb really well - exciting even - and should cruise at the high end of the LSA speed limit on the 80 hp Rotax - we may have to limit the speed with prop adjustments and other tricks. Of course, if built as an Experimental Amateur Built, no speed limits and restrictions. We are also looking at other engine options for the In-line models. The Geo metro engines from Air Trikes and AeroMomentum should be able to fit our P-40 cowling as we intended this to be so. However, we need better dimensional data from the companies to be certain. Doesn't everyone have 3D models now??? The Verner powered Hellcat will climb like a home-sick angel. It has double the torque of the Rotax with the right prop, and there is room to have a large diameter prop on it to use that torque. The drag the F6F will have due to the cowling and barrel-like fuselage is not easy to calculate with our capabilities. So, we will have an idea but no way of knowing how close we are till we fly her.
Also want to re-state that we are not killing the 63% Hellcat - it is just on hold for a bit. We need to get more resources to continue it. We have numerous options but chose to make these Lite Fighters as a way to get us started small and learn the business. I mentioned on the Homebuiltairplanes forum that this is a means to an end - we intend to complete the 63 and other larger two-seat models. Having both product families will be a good thing! Checkout these pics, we will update the whole website soon, but not a huge priority right now. So hit the News page and follow us here. Thanks!!